Problem
A Prefix customer needed a tooling fixture used to apply automotive decals redesigned due to several problems inherent with the existing configuration. The original tool was a multi-piece assembly made up of machined aluminum and nylon, making it sub-optimal for several reasons:
- Considerable weight (15 – 20 lbs. depending on vehicle) causing operator fatigue
- Dimensional inaccuracies from tolerance stack-ups inherent with a multi-part assembly
- Vehicle damage due to difficulty in handling
- Excessive time to make and assemble
Solution
Prefix engineers redesigned the tool so it could be 3D printed, leveraging the technology’s design freedom and lighter materials.
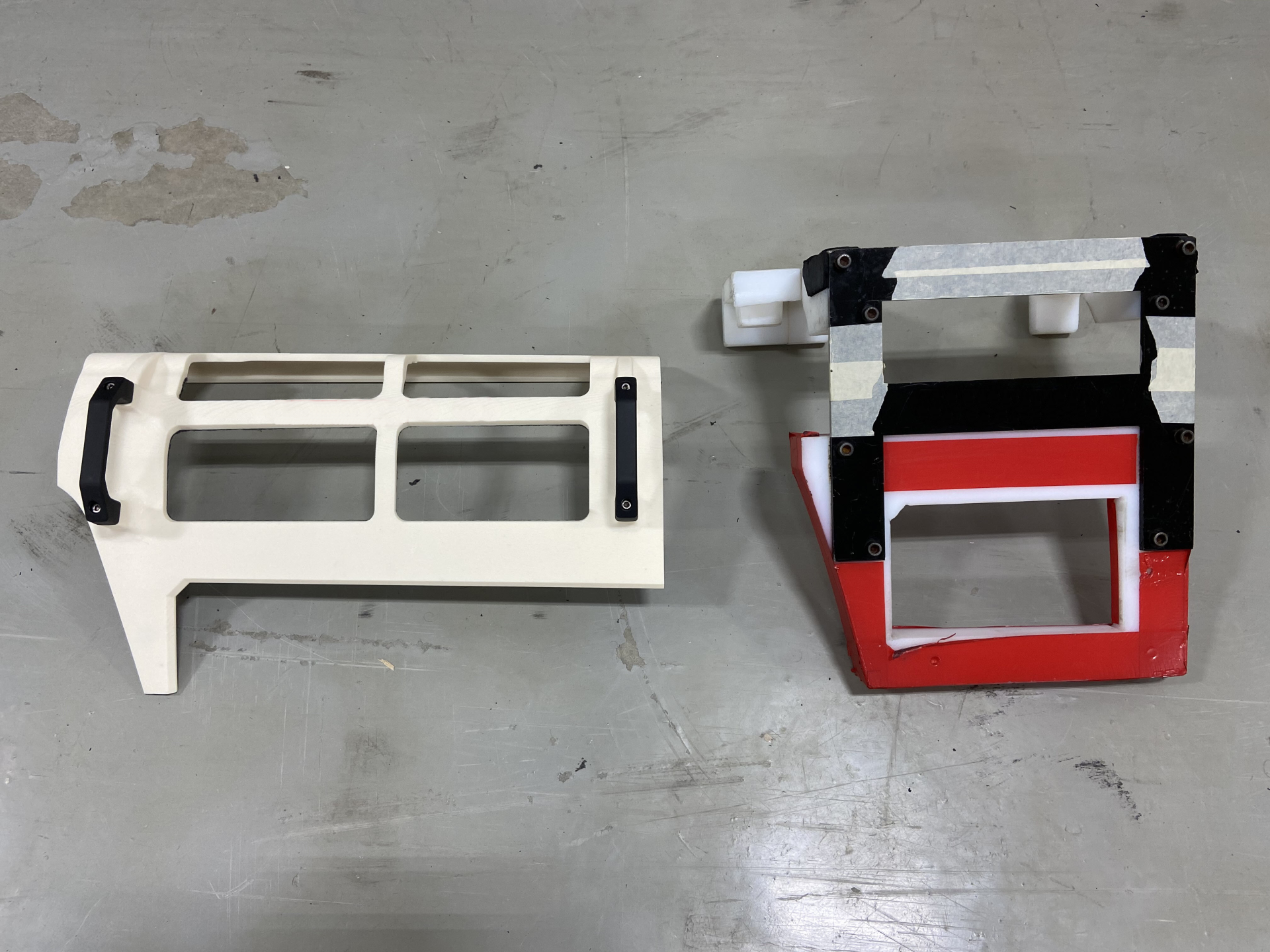
Implementation
The tool was printed using a Stratasys F770 large-format printer, taking advantage of its large 13 cubic-feet build volume. This provided the capability to make the bulk of the tool as a single part and use off-the-shelf handles, avoiding the need to make and assemble multiple pieces.
Outcome
3D printing the redesigned tool using a Stratasys F770 provided several key benefits:
- Over 70% weight reduction affording much easier use
- Single-piece design with accommodation for stock handles, avoiding assembly
- Elimination of positioning inaccuracies from tolerance stack-ups
- Significantly reduced chances of vehicle damage
- Accurate decal placement from better tool positioning due to a more effective design
- 100% first time quality results achieved using the fixture on over 100 units
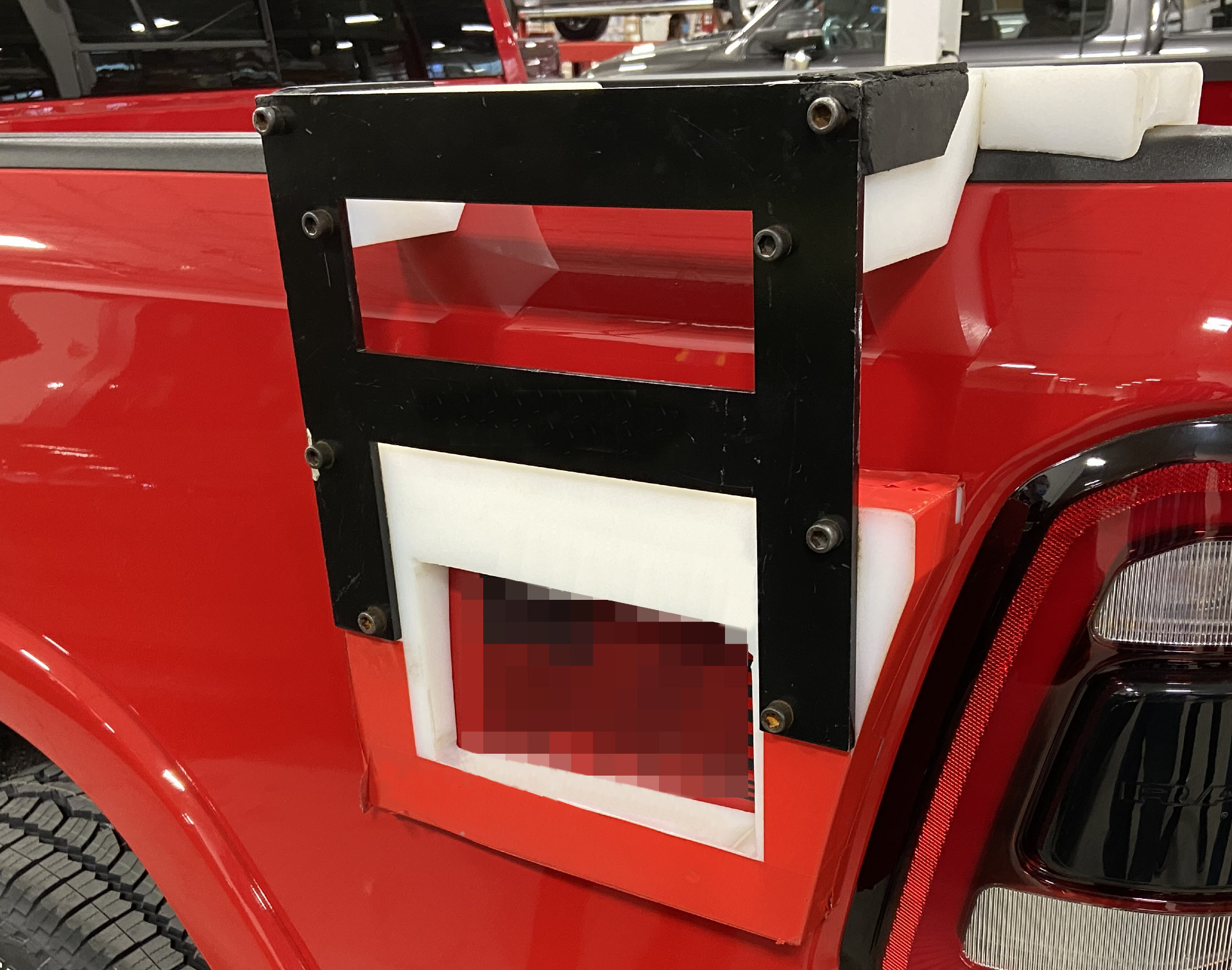