Problem
Access to tourniquets can ultimately decide if wounded soldiers and citizens live or die. With as little as three minutes to stop bleeding from a major wound before death, a reliable supply of tourniquets carries irreplaceable value in war settings. Russia’s recent invasion of Ukraine has disrupted manufacturing supply chains for many critical medical supplies. As a result, the Ukrainian government had a shortage of life-saving tourniquets, putting out an urgent request for assistance. However, the time sensitivity and high urgency of this request posed a unique manufacturing challenge for mass production. Timely production of some of the tourniquet’s main components, such as the clips, would not be possible using traditional manufacturing processes. Requisite tooling must be manufactured before production of the final part can even be started. Relying on injection molding would mean inevitable delays in the ballpark of multiple weeks before the earliest steps of tourniquet production.
Solution
Large, distributed networks of 3D printers are well-equipped for swift emergency response: cloud-based 3D printing software with centralized control allows users to immediately initiate large-scale production across each printer connected to the network. To assist the Ukrainian population in need, Project DIAMOnD activated the world’s largest distributed manufacturing network — which includes over 300 Markforged industrial 3D printers — to fabricate a large quantity of tourniquet clips with a short turnaround time. Automation Alley’s Project DIAMOnD (Distributed, Independent, Agile Manufacturing on Demand) improves local manufacturers’ agility and resiliency by helping them implement digital manufacturing technologies such as 3D printing, while also creating a large-scale emergency response network for printing critical supplies on demand. In exchange for supplying Michigan’s small to mid-sized manufacturers with 3D printers, Project DIAMOnD reserves the right to mobilize the network at any time in response to an emergency need.
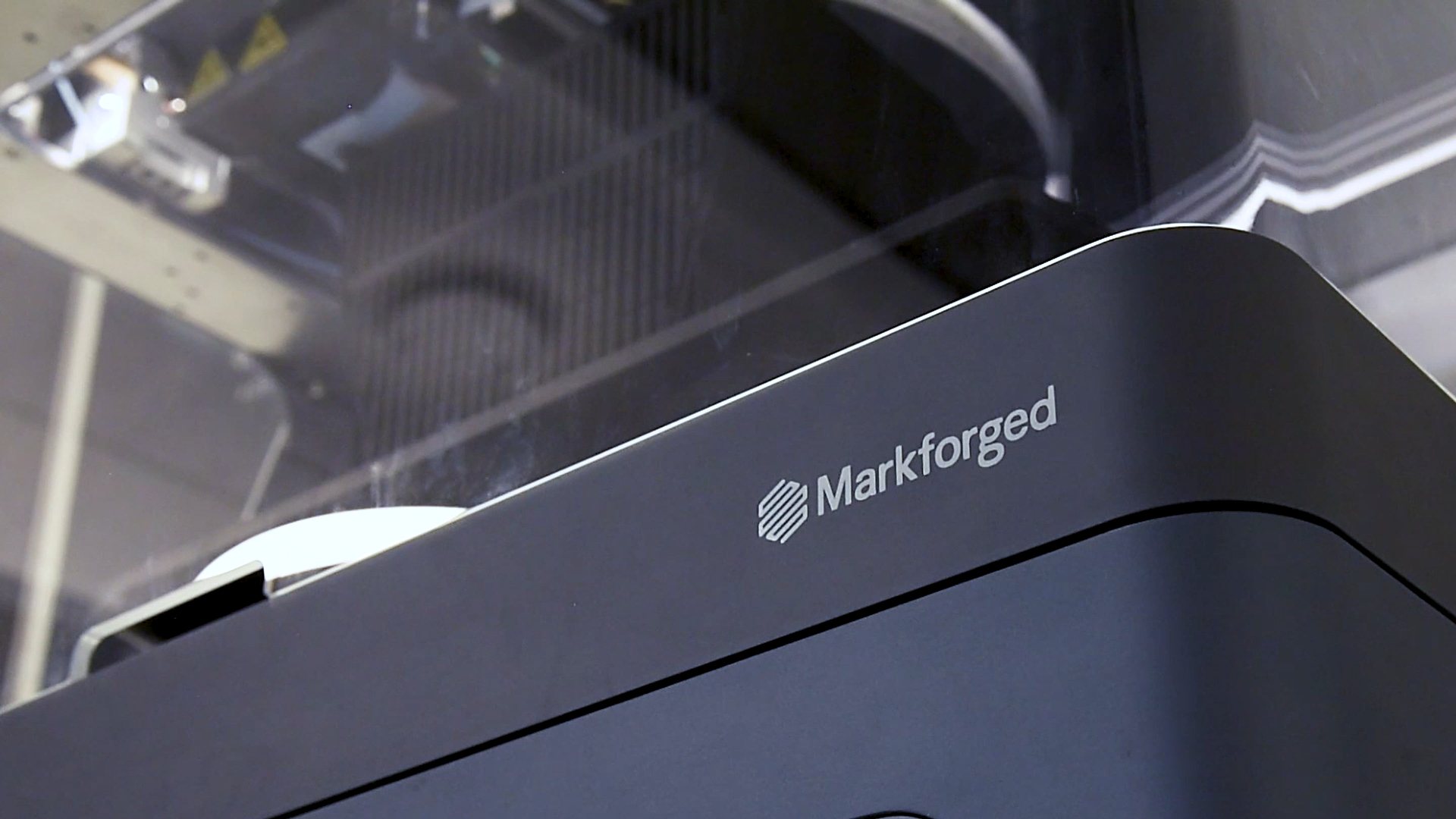
Implementation
Each 3D printer on Project DIAMOnD’s network is connected to a centralized, secure cloud network. This allows manufacturers to use 3D printing software not only for slicing — but also for storing parts as digital inventory, distributing builds, and initiating prints across geographically distributed points of manufacturing. Deployments of this nature are not possible without both cloud connectivity and a software platform specifically designed for distributed manufacturing.
To accommodate the user-friendly workflow needs for an operation of this scale, Markforged used the Eiger API to develop the bespoke Command Center application. Command Center provides centralized control over the network — automating build file distribution and queueing, guaranteeing a print with specific settings is distributed identically across the fleet. To enforce standardization across parts the network prints, Command Center shields its connected printers from decentralized requests to print raw STL files. Decentralized print requests could lead to variations in print settings across the network, resulting in quality, tolerance, and material property discrepancies. With centralized control, one build with a specific configuration can be printed across each machine — which means every member of the network is producing the same part.
After Danish 3D printing organization Makers help designed the 3D printed tourniquet clip, Automation Alley distributed the part’s build to the distributed network of manufacturers across Oakland and Macomb Counties in Michigan for printing. Markforged donated 150 spools of Onyx material for Project DIAMOnD’s network of manufacturers to consume for production of these tourniquet clips.
.jpg)
Outcome
Through Project DIAMOnD, over 7,000 tourniquet clips were distributed through the cloud as digital inventory and printed over the network of Markforged printers. After fabrication in hundreds of locations across the state of Michigan, the tourniquet clips were shipped east and received by the Ukrainian government.
.jpg)
The experience yielded several key learnings. These takeaways represent necessary considerations for successful deployment of any large, distributed manufacturing network, as well as the industry’s path to bringing additive’s supply chain benefits to mainstream use at scale.
- The first takeaway is that readiness of deployment activities is critical to success and must be tested. When working with an interorganizational network involving over 300 stakeholders, users must act swiftly and instinctively, and adhere to planned protocol on a moment’s notice. Lack of procedural readiness can lead to hiccups in execution, compromising uniformity of the finished prints. Understanding that practice makes perfect, Markforged and Automation Alley have since worked together to build a network readiness test to regularly assess and practice mobilization for future emergency activations.
- Effectively satisfying mass production needs with the supply chain benefits of distributed additive manufacturing networks also demands standardization of parts and materials. The value of fast, location-agnostic production is mostly diminished if parts produced aren’t consistently safe, interoperable, and usable. Tools and measures to limit variation — ensuring each part of its kind will perform the same way, no matter where it’s printed — are therefore critical. By leveraging a single software platform to centralize control over a large-scale distributed network, Project DIAMOnD was able to maintain consistent fabrication across each printer and print job — the same part with the same material properties can be produced by every member of the network. Simply sharing out just a design file to be independently configured by over 300 different users will not sufficiently achieve production-level performance and standardization.
Demonstrating material traceability can also ensure end-product quality, by confirming that products are built from materials that have a clear origin, vetted fabrication process, and robust testing history. Beyond traceability, material systems can be qualified through programs such as NCAMP, by providing data on the repeatability of part strengths and performance through exhaustive testing. Smart 3D printing software also exists to limit fabrication-induced variation of parts, using automated part inspection while parts are printing to provide detailed reports on part quality, and if they’re in-spec.
- Digital automation across large, distributed networks isn’t just a speed and efficiency booster for quality control: it permits centralized oversight and record-keeping that wouldn’t be possible if each part was manually inspected or scanned across 300 different locations. While management of intellectual property (IP) was not a constraint to this initiative, commercialized deployments involving proprietary part designs would require security measures to ensure only authorized users at each point of manufacture have access to proprietary part information. Beyond measures such as role-based access control and multi-factor authentication (MFA), this might necessitate providers tailoring user access management to fit organization-specific needs with bespoke software applications, such as Command Center.
This successful activation was ultimately about finding impactful purpose in a test run. This deployment serves as a proof of concept for a future of digitally connected supply chains, where large-scale networks drive on-demand production to points of need anywhere across the globe. Additive’s unique ability to solve this time-sensitive manufacturing challenge is evidence. Even without production at the point of need, printing the clips in Michigan and shipping them 5,000 miles still allowed a far faster and more efficient delivery than injection molding closer to eastern Europe. This test run’s learnings yielded not just a bright prognosis for the world’s supply chains — but also a valuable industry roadmap for achieving widespread, commercialized use in even the most stringently regulated manufacturing fields, such as aerospace.
As Automation Alley and Markforged build on this deployment’s strengths to perfect this proof of concept, expect to see similar distributed additive manufacturing networks print the solutions to even more challenging supply chain problems.