Overview
Distributed manufacturing generally refers to manufacturing performed in a geographically dispersed manner, at small scales, close to the end user. It stands in contrast with centralized manufacturing in large factories, often far away from the end user, which is the predominant mode of manufacturing today. However, the concept of distributed manufacturing is not new. In fact, some have argued that it is the original mode of manufacturing, carried out by artisans for centuries before the First Industrial Revolution [1]. Nevertheless, over the past decade or two, modern concepts of distributed manufacturing have been gaining increasing attention and traction. This white paper delves into the mindset shifts, the business models, and the digital tools/innovations driving distributed manufacturing in the modern era, concluding with an outlook for the future.
Mindset shifts
The transition from distributed to more centralized forms of manufacturing started with the First Industrial Revolution in the 18 century, driven by mechanization and steam power. During this period, the factory system involving specialized establishments and machinery gradually took the place of craft production carried out domestically or in local workshops using hand tools. The second and third industrial revolutions only amplified this trend towards centralization with the advent of electrification, mass production and automation. However, the fourth industrial revolution (or Industry 4.0) underpinned by advancements in cyberinfrastructure, information and communication technologies, has opened up unprecedented opportunities to network people and resources dispersed all over the world, paving the way for a modern era of distributed manufacturing.
However, besides technology, there are several socio-economic trends driving a transition to distributed manufacturing. They include consumer tastes, geopolitical and environmental concerns, and some of the disruptions caused by the recent pandemic, including its impacts on the supply chains of a wide range of industries.
Consumer tastes are changing. At the turn of the 20th century, Henry Ford exploited the efficiencies of centralized manufacturing through mass production to democratize a product – the automobile. The caveat was, however, that any customer could have a car painted any color that he or she wanted so long as it was black! As a result, in 1918, half of all the cars in the United States were Model T’s; most of which were painted black [2].
A lot has changed since then. Today’s consumers increasingly expect highly personalized products on-demand. For example, there are now over a million variations of automobiles available to the U.S. consumer [2]. This growing trend away from mass production to what is known as mass customization is not confined to the automotive industry; it is a widespread phenomenon. Mass customization is formally defined as the production of goods and services to meet individual customer’s needs with near mass production efficiency [3]. It combines the flexibility and personalization of “custom-made” with the low unit costs associated with mass production. Centralized manufacturing paradigms are better attuned to mass production, hence there is a hunger for alternative forms of manufacturing that can better handle the demands of mass customization.
Linked with demands for customization is a renaissance of the type of artisan culture that marked the original forms of distributed manufacturing. For example, there is a growing culture of “making” as opposed to passive consumption [4]. As a result, so-called makerspaces – i.e., open-access manufacturing workshops – are becoming prevalent. This trend has led to the term “prosumer,” referring to consumers who are also producers, opening up opportunities for grassroots versions of distributed manufacturing, where not only are products democratized but production itself is democratized [5].
Geopolitical and environmental concerns are also fueling a reconsideration of centralized manufacturing, particularly forms of it that involve offshoring of manufacturing. Over the last couple of decades, there was a growing trend in more developed countries to offshore manufacturing to large factories located in less developed countries to cut production costs. However, these practices have come at a cost to the more developed countries by raising the anxiety of blue-collar workers who have seen their livelihoods decimated causing political upheavals. Off-shoring has also led to growing concerns around national security and environmental pollution caused by the need to ship raw materials and finished products over long distances to reach the manufacturers or end users. As a result, there is a strong push to re-shore and distribute manufacturing to struggling communities that have borne the brunt of off-shoring in developed countries.
Perhaps one of the greatest catalysts for distributed manufacturing in recent years has been the COVID-19 pandemic and its aftermath. The pandemic has unearthed a variety of vulnerabilities with the current centralized paradigm of manufacturing, including its lack of agility, flexibility and resiliency, causing lots of companies and governments to start re-evaluating the status quo. Simultaneously, the pandemic has shed light on the potential of distributed manufacturing to help alleviate some of the identified vulnerabilities. Perhaps one of the more vivid examples of this was during the early days of the pandemic when there were severe shortages of personal protective equipment (PPE) to help stop the spread of the coronavirus. Many factories were unable to react quickly enough to meet the sudden surge in demand for PPE; but individuals and small businesses dispersed all across the world were able to react much quicker to manufacture various types of PPE to fill the gap while mass production ramped up. Moreover, the pandemic revealed the potency of digital tools, like video conferencing, to keep economies humming even in the presence of major disruptions. In the aftermath of COVID-19, persisting supply chain issues are putting pressure on companies to adopt digital tools and diversify their supply chains to improve agility, flexibility and resiliency.
Business Models
There are many ways to categorize business models for distributed manufacturing, but, in this white paper, we choose to categorize them in relation to their degree of democratization, i.e., the extent to which they engage a network of geographically dispersed individuals or groups of individuals as free-agents in distributed manufacturing activities. This is based on the author’s opinion, also shared by others [, that distributed manufacturing is at its best when it also fosters democratization of manufacturing.
Model 1: Undemocratized Distributed Manufacturing
This model is a direct offshoot of the centralized manufacturing paradigm where companies – usually large multinational companies – distribute production such that they are closer to the end user. This form of distributed manufacturing is undemocratized because the geographically dispersed production sites are still owned and/or controlled by the parent organization. In this model, a lot of the benefits of distributed manufacturing accrue to the parent company but the distributed production could create local employment and opportunities for suppliers at their various sites. Within this model, one can find several different variants. For example, the distributed sites could be homogenous, where the sites are essentially designed to manufacture the same product in various locations with almost exactly the same set up. Alternatively, they could be customized for each location and highly adaptive to cater to the local demands at the given site. This model can be extrapolated to a future distributed manufacturing model where a few large companies own thousands if not millions of networked local manufacturing sites, packed with robots that carry out manufacturing all day long. They will certainly be distributed but have little or no democratization.
Model 2: Partially democratized distributed manufacturing
This is the model we see in emerging manufacturing-as-a-service companies like Xometry, Protolabs/Hubs, Fast Radius, etc. It is a one-to-many model in terms of the business relationship. A parent company receives manufacturing orders from clients and distributes the orders to a network of geographically dispersed production sites, mostly small and medium-sized enterprises, close to the end user. A major difference from Model 1 above is that the companies that fulfill the orders are independently owned and operated. Therefore, it provides opportunities for some level of profit sharing between the parent company and its network of manufacturers, though it is likely that most of the profit accrues to the parent company. This model is gaining a lot of traction. For example, some of the parent companies that have adopted this model have a few thousand manufacturers in their network. One can imagine a future where this model continues to scale to a point where a parent company could have hundreds of thousands of small and medium sized manufacturers in their network.
Model 3: Fully democratized distributed manufacturing
This is arguably the holy grail of distributed manufacturing. It is a model of distributed manufacturing that is “for and by the masses [6].” The participants in this model are, for the most part, free agents in a peer-to-peer relationship. One can imagine software platforms that connect the participants – both clients and manufacturers – to each other and helps to streamline transactions. However, the platforms do not dictate the negotiations nor interactions among the participants. A variety of Industry 4.0 technologies could be used to facilitate contracts, traceability, quality control, etc., together with regulations and policies to guide the business dealings. The manufacturers and clients that participate in this model could be individuals, small and medium-sized or large enterprises. Versions of this model have been proposed as concepts under various names, e.g., commons-based peer production [7] and social manufacturing [8]. However, it is yet to be realized in the manufacturing industry, though one can see flourishing forms of this model in other industries, e.g., peer-to-peer marketplaces like AirBnB, Etsy, and Uber.
Digital Tools and Innovations
The major technologies involved in Industry 4.0 are drivers of distributed manufacturing to varying extents. A few examples are highlighted below.
Cloud computing: This is a model for enabling ubiquitous, convenient, on-demand network access to a shared pool of configurable computing resources that can be rapidly provisioned and released with minimal management effort or service provider interaction [9]. Cloud platforms are critical to distributed manufacturing, as they enable easy sharing, processing and storage of digital information. Cloud computing has proved to be a key enabler for Business Model 2 described above, and is indispensable for Business Model 3 [6].
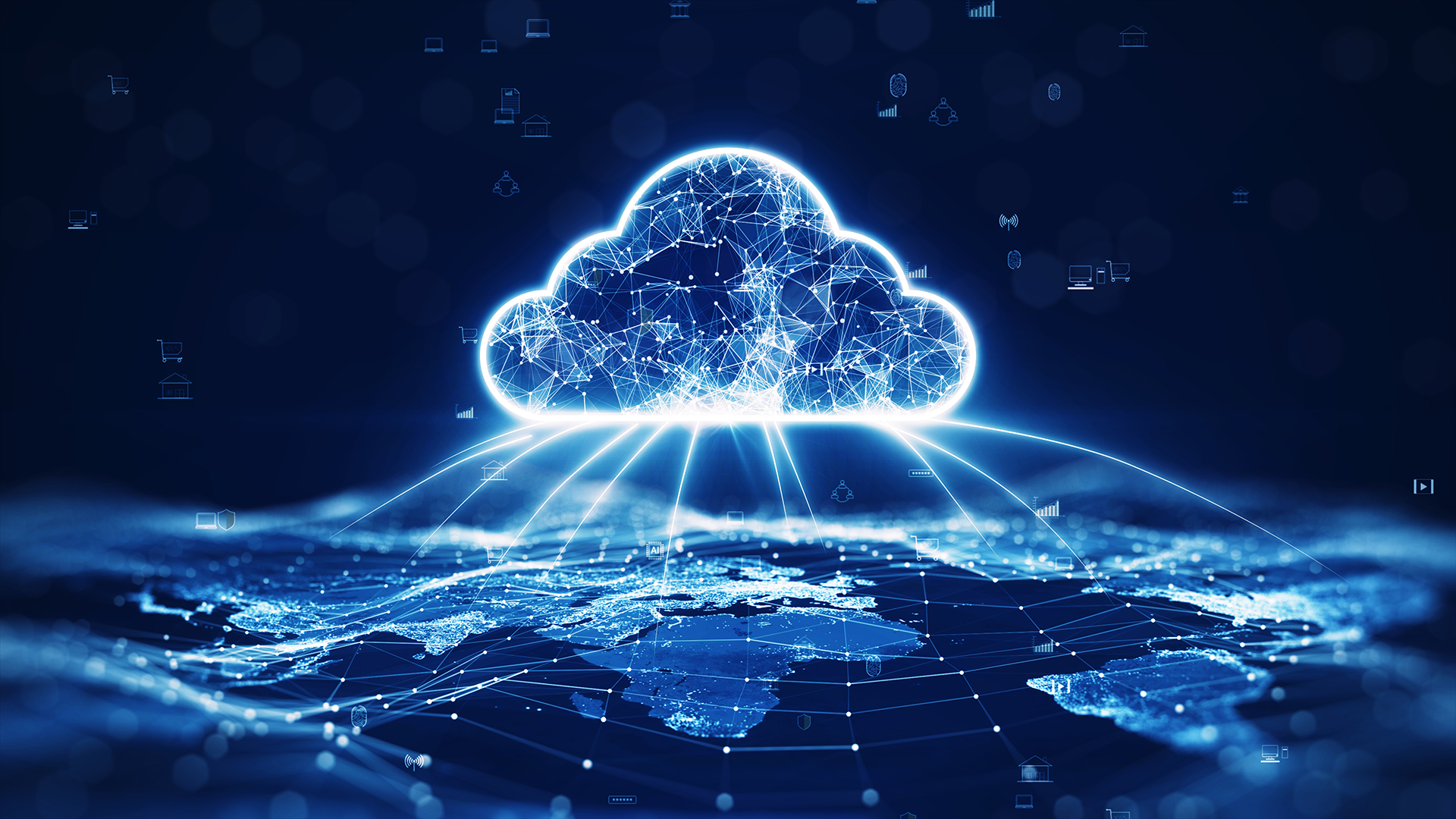
Additive manufacturing: Additive manufacturing (AM), also known as 3D printing, is a manufacturing process that builds parts directly from 3D model data, usually by joining material layer upon layer, under automatic guidance from a computer. AM facilitates distributed manufacturing in several ways. For example, AM is suited for low-volume, customized manufacturing because it does not require much (if any) of tooling and it relaxes a lot of design constraints of traditional manufacturing. This allows AM to be used for on-demand manufacturing in small lot sizes. As a result, AM enables companies like 3YOURMIND to create digital inventories of parts that can be produced on demand. Another way AM facilitates distributed manufacturing is through the ubiquity of low-cost 3D printers that make it possible to engage large swaths of the population in manufacturing, thus facilitating democratization of manufacturing, as in Business Model 3 above.
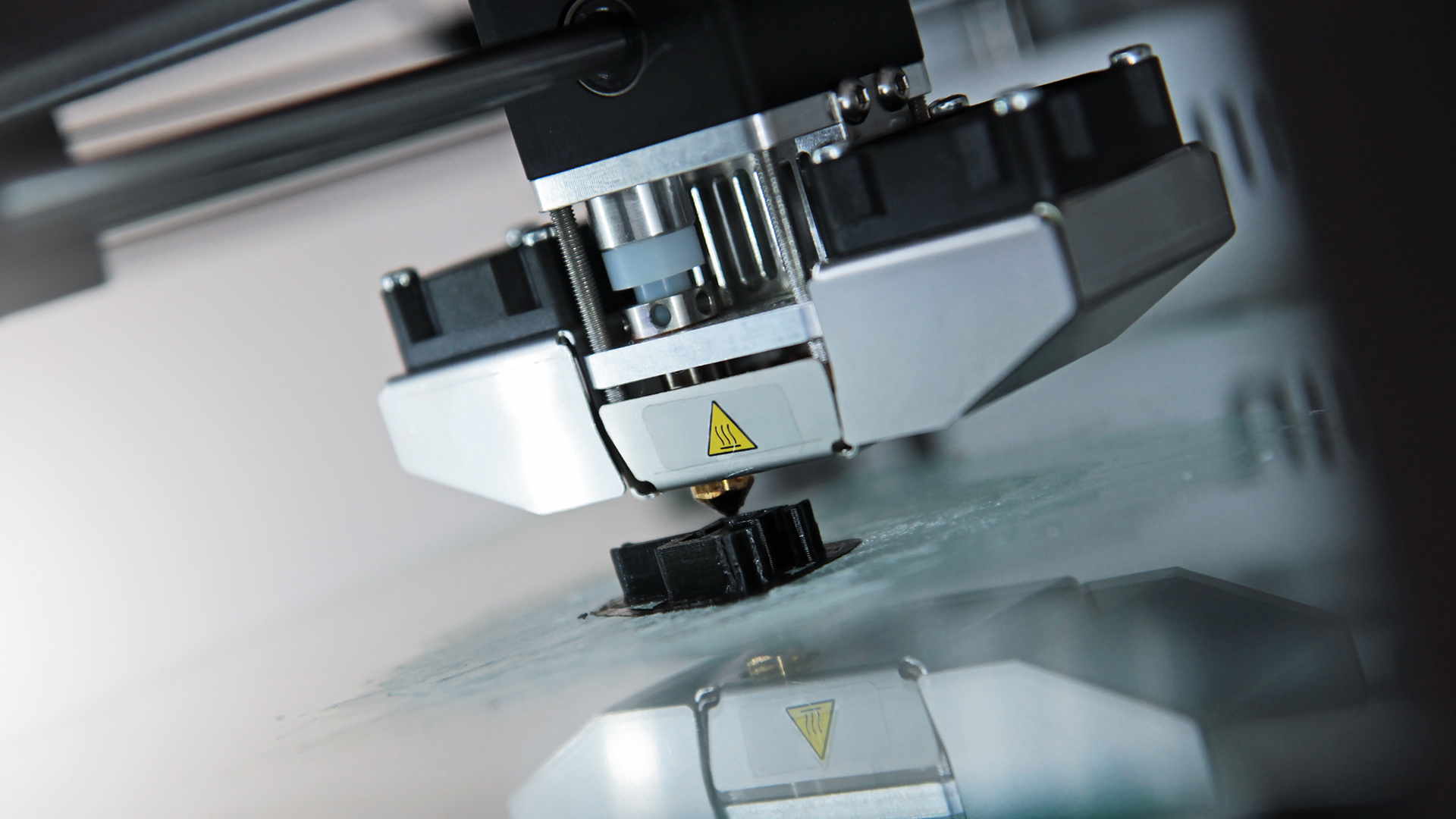
Artificial Intelligence and Machine Learning: Artificial intelligence (AI) is a broad field encapsulating a variety of techniques that enable computers (and machines in general) to mimic human intelligence. Machine learning (ML) is a subset of AI that enables computers to learn from experience (data). These technologies are enabling distributed manufacturing platforms to develop useful models from the data gathered from the transactions that occur on their platforms. Such models could be used, for instance, to forecast demand, predict quality as a function of location, and ultimately optimize the networked manufacturing system. AI and ML could also help match manufacturing jobs to capabilities in a network of distributed manufacturers and assist a client to fix their design such that it is manufacturable, to name a few.
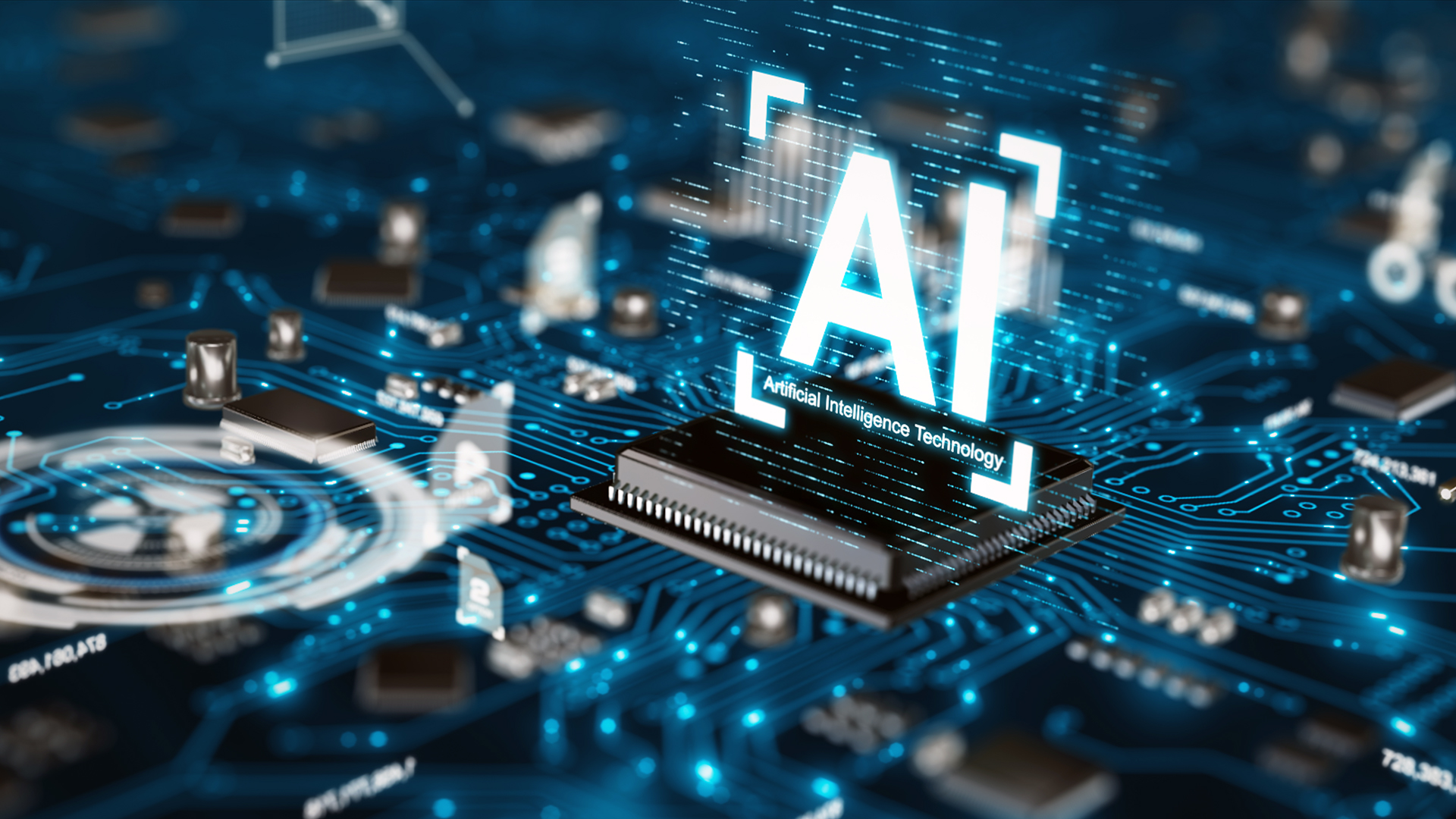
Internet of Things: The Internet of things (IoT) describes the network of physical devices that are embedded with capabilities that enable them to connect and communicate with one another over the internet. When applied to the industrial sector (e.g., manufacturing), IoT is referred to as industrial IoT (or IIoT). IoT allows the myriad of agents involved in distributed manufacturing to easily connect and communicate with one another. For example, a factory can keep track of the delivery status of raw materials and adapt its operations accordingly. IoT can make geographically dispersed entities to act as a cohesive unit through networking and communication.
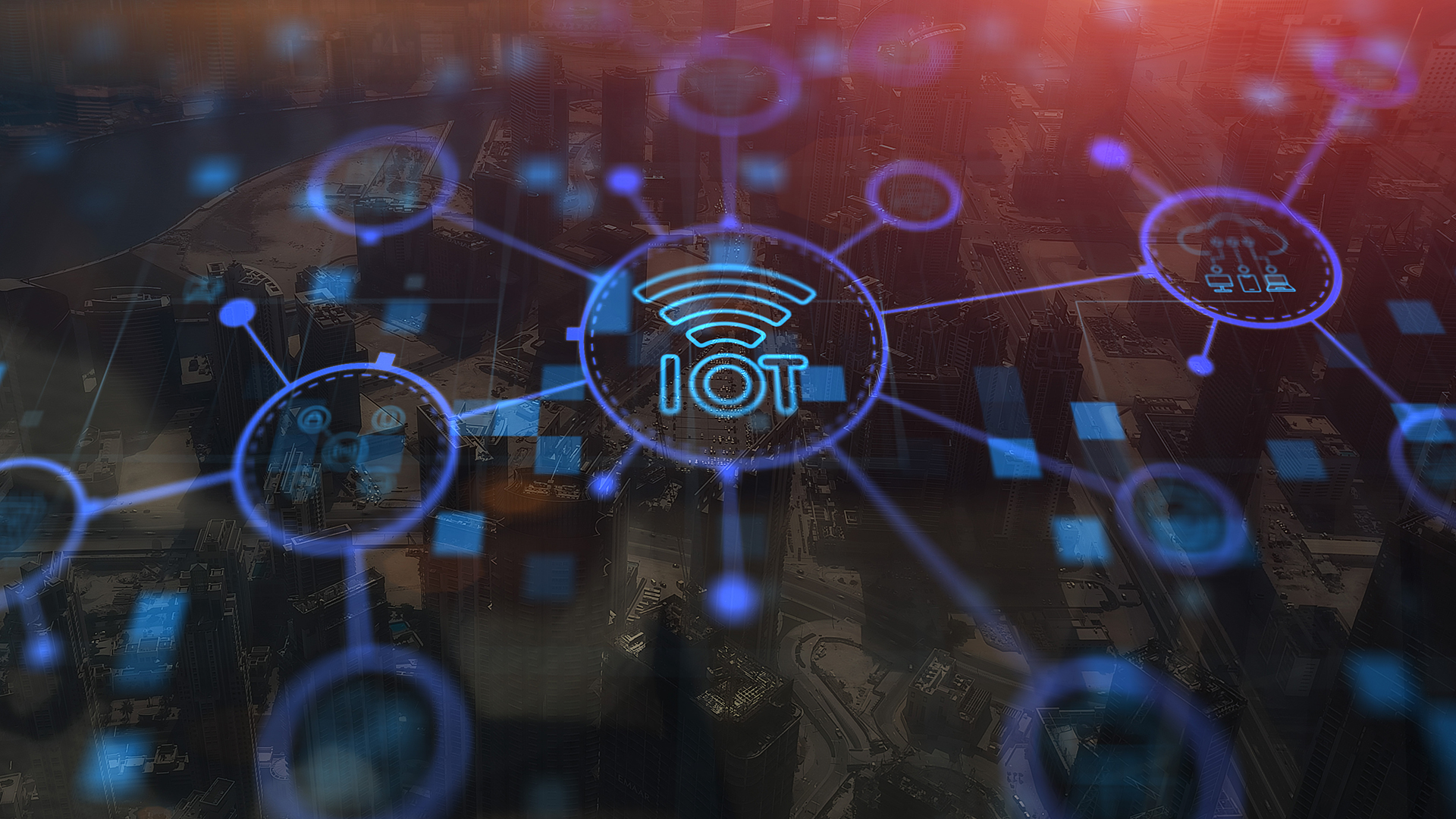
Robotics: This involves the design, construction, operation, and use of machines with embodied intelligence that can help and assist humans. Robotics can facilitate distributed manufacturing in a variety of ways. For example, collaborative robots can work alongside a human to support them in, say, packaging. Delivery robots (like drones) could be used to facilitate logistics across geographically dispersed manufacturers. Inspection robots could be used for quality assurance to remove the variability that comes with human inspection, hence help to assure quality across a network of manufacturers.
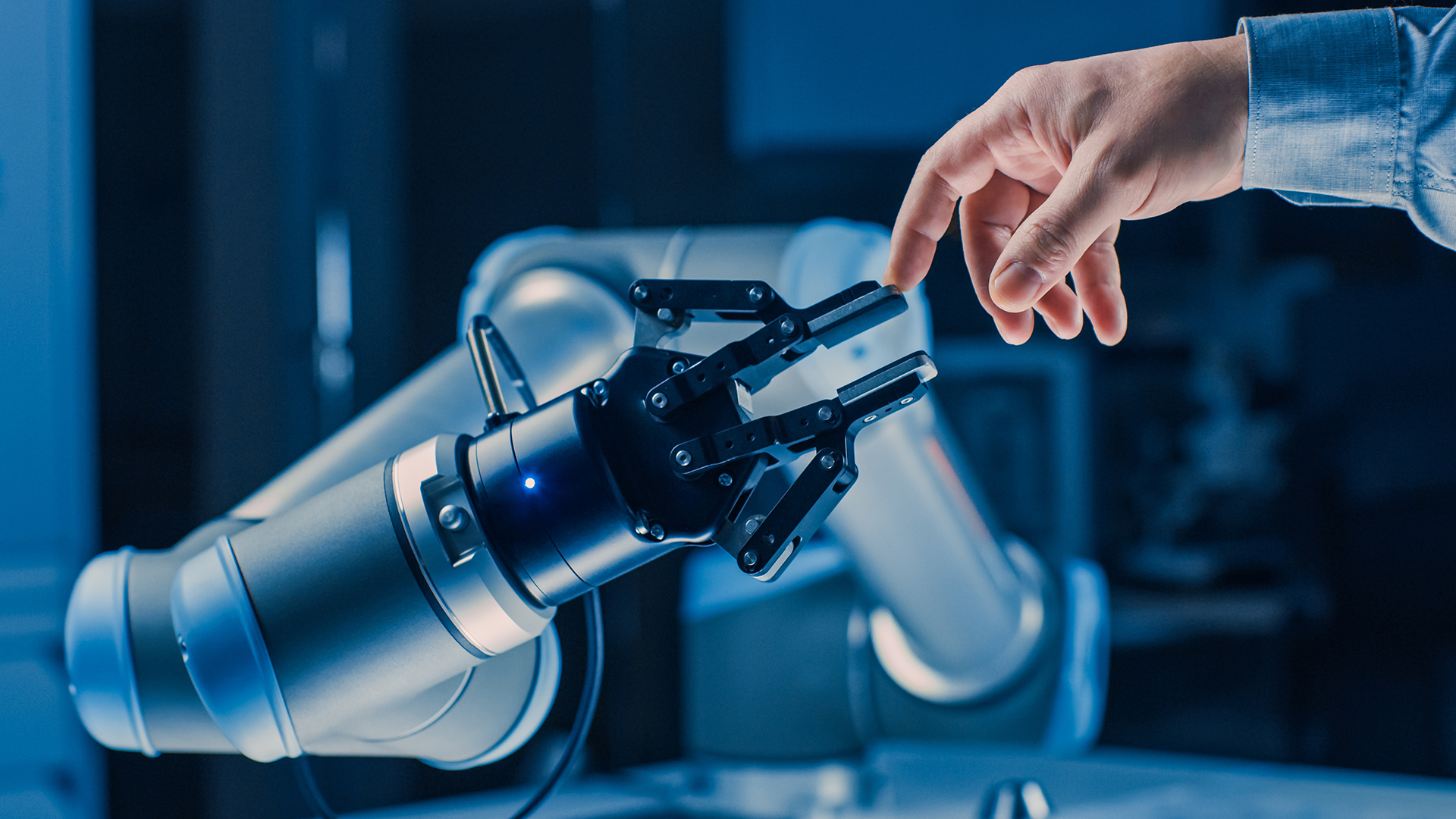
Cybersecurity: This is the protection of computer systems and networks from malicious activities. It is an extremely important driver of distributed manufacturing because of the increased surfaces for attack created by the supporting network. Privacy and confidentiality are related concepts to cybersecurity. In a distributed manufacturing environment, it is important to be able to share information with a network while maintaining privacy and confidentiality. Encryption and distributed ledgers (blockchain) are some of the technologies that can support security, privacy and confidentiality.
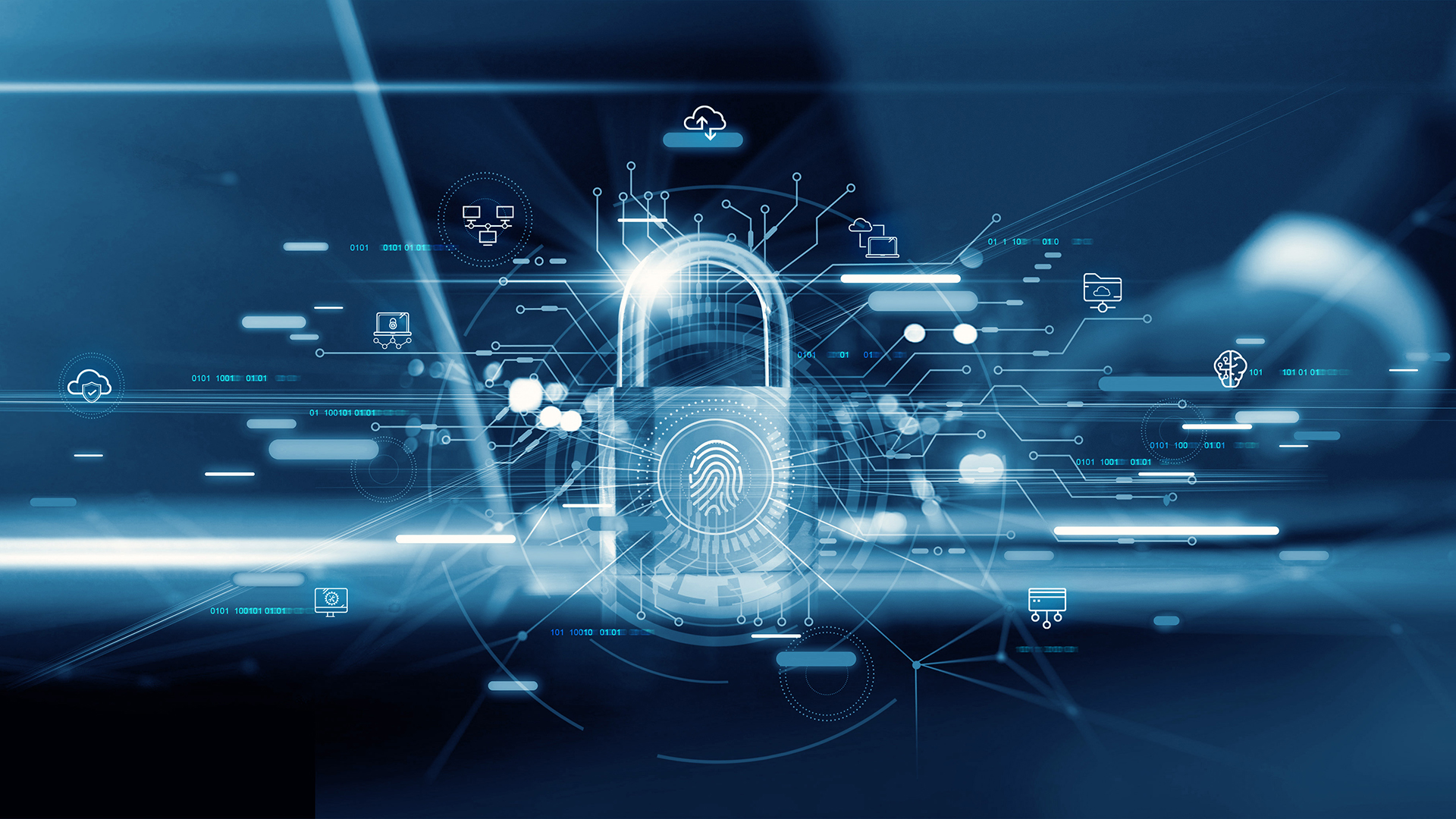
Next Steps
Distributed manufacturing is experiencing a renaissance fueled by Industry 4.0 technologies combined with changes in consumer behavior, geopolitical and environmental concerns. The recent pandemic and its aftermath – e.g., supply chain disruptions – have only helped accelerate the quest for distributed manufacturing. A variety of business models are possible within distributed manufacturing. However, we argue that to reap the full benefits of distributed manufacturing, technologies, policies, and other infrastructure must be trained toward incorporating democratization into distributed manufacturing. From a technological standpoint, the building blocks for democratized models of distributed manufacturing already exist in Industry 4.0 – e.g., cloud computing, additive manufacturing, artificial intelligence and machine learning, IoT, robotics, and cybersecurity. However, these technologies must be harnessed to create frameworks that enable the expansion of distributed manufacturing. For example, four of such frameworks that have been articulated by Automation Alley’s Project DIAMOnD (Distributed Independent and Agile Manufacturing On Demand) are:
- Global ID: A framework where manufacturers are recognizable via an international identification system, enabling collaboration, trust and quality across continents.
- Digital rights management: A framework that allows the industry to identify the universal ownership and access rights to digital assets distributed across the ecosystem. This promotes scaling and credibility of distributed manufacturing.
- Quality & certification: A standardized quality and Certification framework that provides a mechanism to ensure and verify that components produced across multiple locations are functionally equivalent.
- Product recipes: A product recipe framework that provides a universally accepted mechanism to ensure that components manufactured in a distributed environment are functionally equivalent.
These and other relevant frameworks should be developed through public private partnerships. The ultimate goal should be to enable a paradigm of distributed manufacturing that is economically, environmentally and socially sustainable.
About the Author:
Chinedum (Chi) Okwudire is an associate professor of Mechanical Engineering and Miller Faculty Scholar at the University of Michigan. Prior to joining Michigan, he was the mechatronic systems optimization team leader at DMG Mori USA. His research is focused on exploiting knowledge at the intersection of machine design, control and computing to boost the performance of manufacturing automation systems at low cost. His research has been applied to precision machine tools, nanopositioning systems, wafer scanners and 3D printers. His scholarly and teaching contributions have been recognized by several awards that include the CAREER Award from the National Science Foundation; the Young Investigator Award from the International Symposium on Flexible Automation; the Outstanding Young Manufacturing Engineer Award from SME; the Ralph Teetor Educational Award from SAE International; the Department Achievement Award from the Mechanical Engineering Department, University of Michigan; and the Russell Severance Springer Visiting Professorship at UC Berkeley. He has co-authored a number of best paper award winning papers, including the 2016 ASME Dynamic Systems and Controls Division’s Best Paper on Mechatronics Award, a 2021 IEEE/ASME Transactions on Mechatronics Best Paper Finalist Award, and the Best Paper Award at the 2022 IEEE/ASME International Conference on Advanced Intelligent Mechatronics. He was recently selected by SME as one of the 25 leaders transforming manufacturing.
References
- Srai, J. S., Kumar, M., Graham, G., Phillips, W., Tooze, J., Ford, S., Beecher, P., Raj, B., Gregory, M., Ravi, T.B., Neely, A., Shankar, R., Charnley, F., & Tiwari, A. (2016). Distributed manufacturing: scope, challenges and opportunities. International Journal of Production Research, 54(23), 6917–6935. doi: 10.1080/00207543.2016.1192302
- Eliason, E. 3 Reasons Why Mass Customization is the Future of Consumer Products. Huffingtonpost.com. http://www.huffingtonpost.com/erik-eliason/mass-customization_b_1313875.html (accessed May 28, 2016).
- Tseng, M. M., Jiao, J., & Merchant, M. E. (1996). Design for mass customization. CIRP Annals-Manufacturing Technology, 45(1), 153-156
- Stewart, H., & Tooze, J. (2015). Future Makespaces and redistributed manufacturing. Making futures, 4, 1-9.
- MForesight. (2017, September 21). Democratizing Manufacturing: How to realize the promise of the Maker Movement. Retrieved May 21, 2020, from https://medium.com/@MForesight/democratizing-manufacturing-cf54a47cd2f3
- Okwudire, C. E., & Madhyastha, H. V. (2021). Distributed manufacturing for and by the masses. Science, 372(6540), 341-342.
- Benkler, Y., & Nissenbaum, H. (2006). Commons‐based peer production and virtue. Journal of political philosophy, 14(4), 394-419.
- Jiang, P., Leng, J., Ding, K., Gu, P., & Koren, Y. (2016). Social manufacturing as a sustainable paradigm for mass individualization. Proceedings of the Institution of Mechanical Engineers, Part B: Journal of Engineering Manufacture, 230(10), 1961-1968.
- Mell, P., & Grance, T. (2011). The NIST definition of cloud computing. http://faculty.winthrop.edu/domanm/csci411/Handouts/NIST.pdf Accessed on November 20, 2018