The hiss of steam, hum of churning machines, and a fragrant aroma of hops provides the greeting to Bell's Brewery production facility in Comstock, MI. The complex, which spans 200,000 square feet, brews more than 20 beers for distribution as the national production backbone of the Bell’s brand.
On March 6, 2023, Automation Alley partnered with Southwest Michigan First to facilitate a tour of the state-of-the-art production facility, showcasing how Bell’s brews in Industry 4.0. Over 50 members of Michigan's manufacturing community attended, split into a total of three tours. Attendees were able to see advanced automation, how data drives beer making decisions and how one of the largest breweries in the nation operates with sustainability in mind.
Though a large portion of today’s beer production at Bell’s is streamlined, automated and optimized, the connection to Bell’s craft brewing past is woven through the sprawling production facility. The 15-gallon soup pot that founder Larry Bell brewed beer in throughout the early 1980s is adorned front and center as the starting point of any brewing tour as a testament to his innovation and ingenuity. Today, the facility still maintains a significant research and development focus where Bell’s hand-crafted artistry of beer recipe making, batch brewing and free-spirited tweaking of flavors lives on.
Room for Experimentation
Bell’s Brewery tour guide Ray Bristol shared that the company built their existing infrastructure, considered a “brewer’s paradise,” to allow the production team to experiment with new ways of brewing. “Despite having large brewhouses, high speed packaging lines, and cellars full of big tanks, we still maintain a small brewing system with dedicated brewers, recipe writers and a brewmaster,” Bristol said.
“Bell’s is looking at the marketplace as well as dusting off old recipes in historical styles. We are also looking at things made before prohibition thinking ‘If that is a cool beer, we want to make that.’”
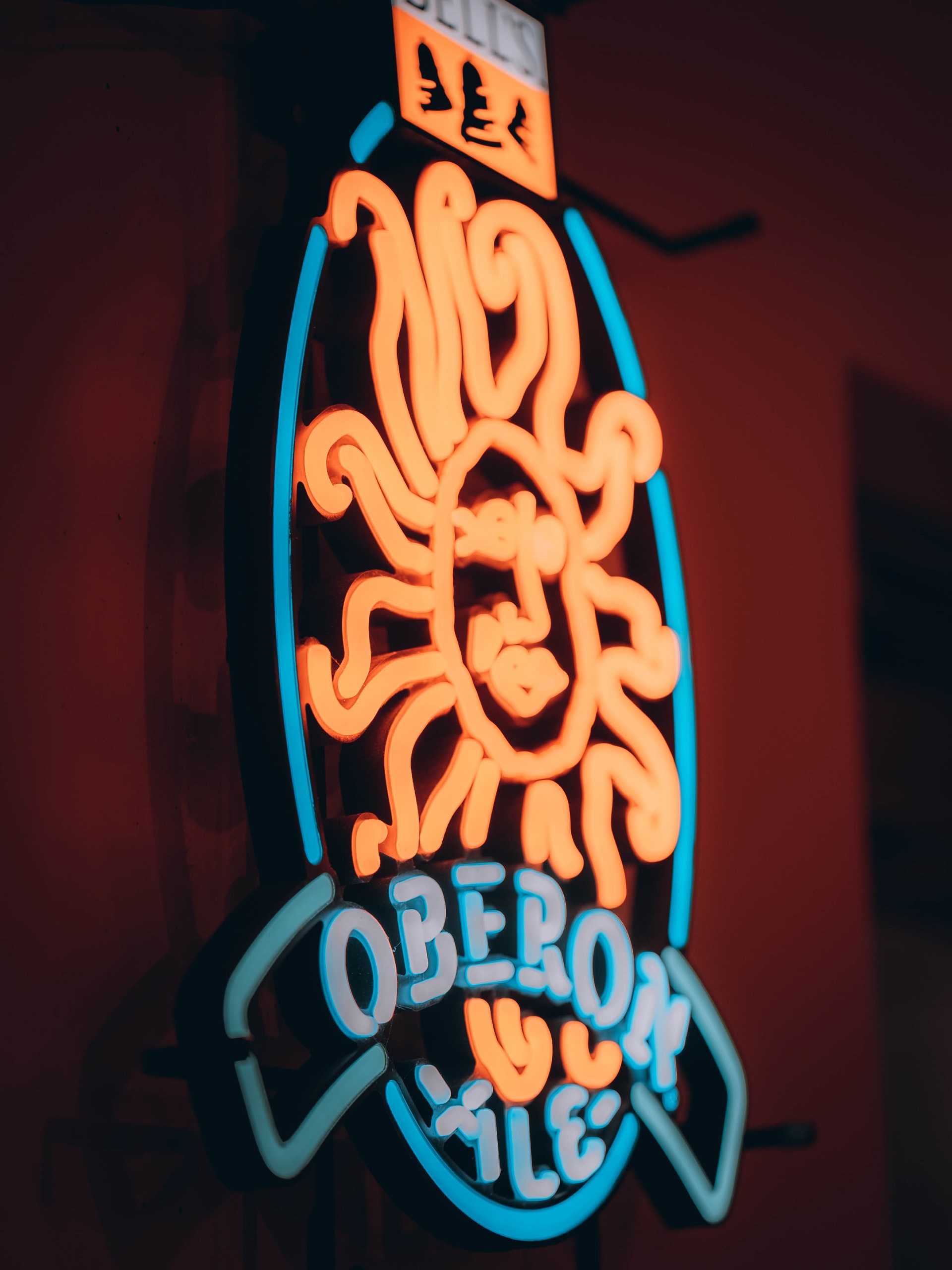
The team relies on a small scale 12 barrel system to prototype new beers. However, the small system is outfitted with the highest standard of brewing technology in the industry.
“There’s no reason for this small of a brewhouse to have the level of sophistication it has, except for the fact that it mimics all the same processes we have in our 200 barrel brewhouse,” Bell’s site engineering manager Dave Sippel said. “This way the beers made on this system will be representative when we scale up.”
The next daily brand of Bell’s beer will likely be made on this system, Bristol said.
“We want to have fun with it, see what sticks,” Bristol added. “This team has the spirit of craft brewing even in a facility like this. We are very blessed to have both sides of the equation.”
Automation in Action
Focusing on the production side of things, the Bell’s facility has all the hallmarks of a modern industrial manufacturer, including a centralized control room flush with data sets, automated systems and advanced robotics.
Empty bottles and cans neatly clink together down separate conveyor belts until being infused with Bell’s beer at automated filling stations. The most visual example of cutting-edge technology at work is the brewhouse’s keg lifting and palletizing robots.
“We have the robot arms that replaced the human power of having to move kegs. Same with empty cans, full cans and full cases. Same with empty bottles, full bottles and full cases. All of these things our automated systems do to prevent the repetition and wear and tear on the human body,” Bristol said.
One robot arm flips kegs to the upright state after they are filled. The other neatly stacks pallets of beer set for shipping out across the country.
“Prior to this we were more limited in throughput because it required someone using human power to flip kegs. . .Obviously, this is really tough on the body and nobody wanted to do this for a long period of time. So we didn’t run at the same rate we are able to run at today,” Bristol said.
Aside from efficiency gains, the automation of this process enabled Bell’s to increase the size of its workforce, Bristol added.
“Once we got the robot arm in place we were able to add a second shift as a result of putting this automation in. Compared to what people’s mindsets are that you take jobs away, we actually sped up our production and were able to add more jobs to our workforce.”
On the digital side of automation, Sippel said he could run most of the brewery on his phone while lying on the couch at home.
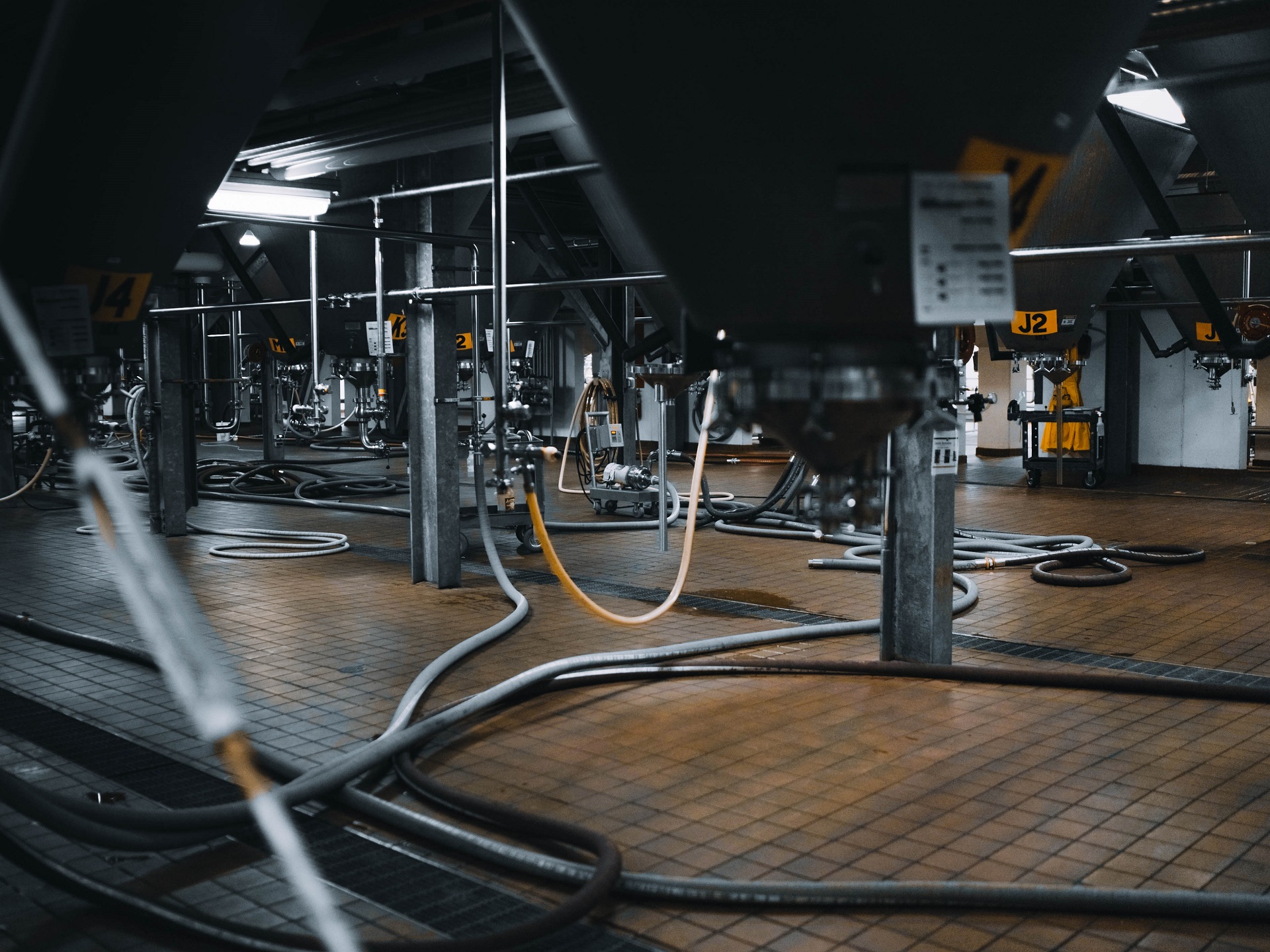
“In a lot of ways Automation can make it feel like you are playing [a video game like] Sim Brewer,” Sippel said. “It is very easy to forget you are controlling very real processes that can be really dangerous.” Operating with safety in mind in the digital realm is key, but it is also important to be present in the room, he added. “You still need to have physical eyes and ears in the process.”
Sustainability Matters
Bell’s Comstock facility is more than meets the eye. The brewery features an 85-ton geothermal field installed eight feet beneath its two-acre hop yard, using glycol filled tubes to exchange heat and offset HVAC demand in the brewery’s offices.
Additionally, the LED lights installed at the brewery conserve 180,000 kWh of electricity per year in comparison to incandescent bulbs— that’s enough electricity to power 22 homes in one year.
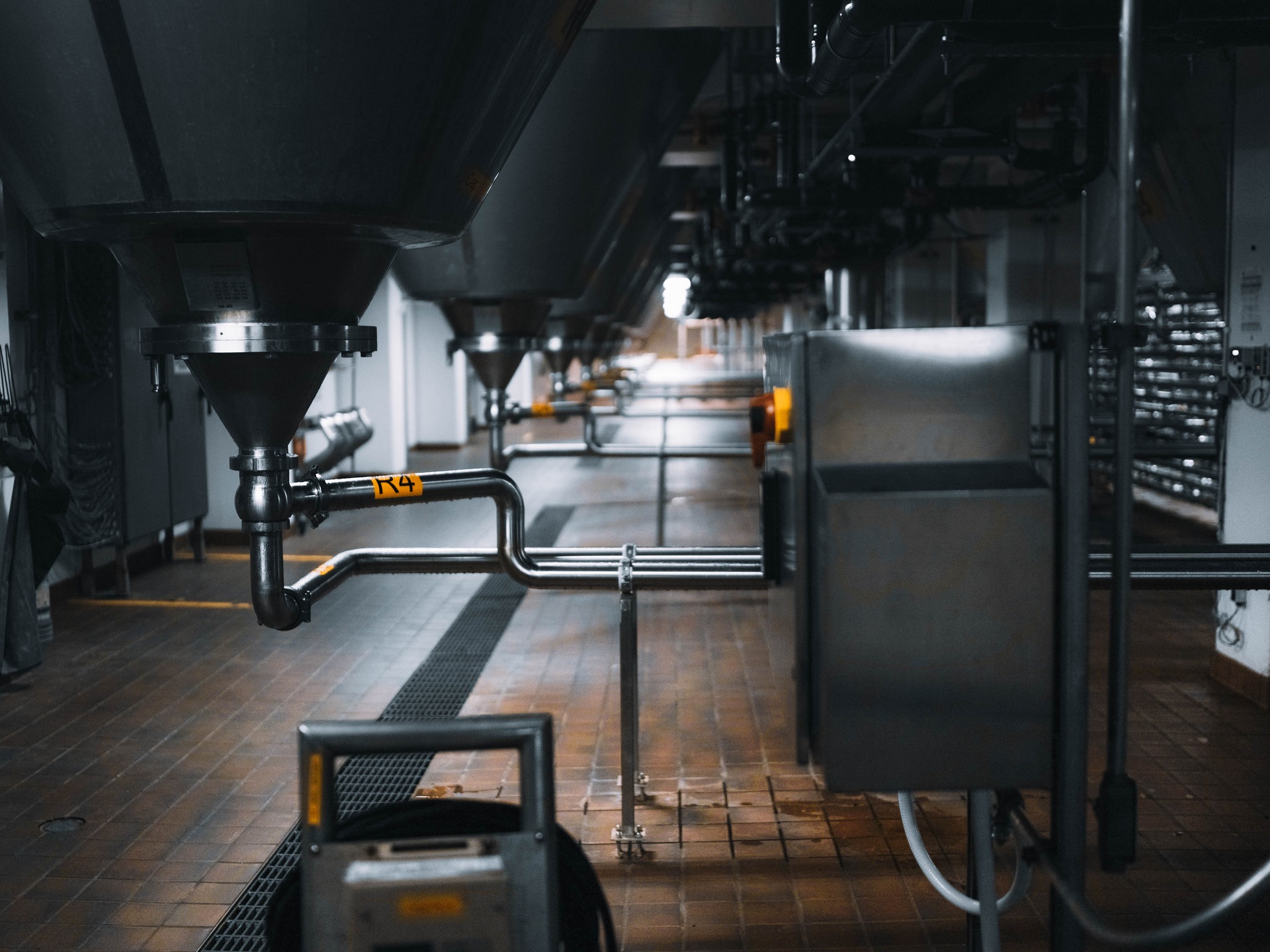
“A lot of the stuff we’ve done to improve the facility has been driven by water efficiency, energy efficiency and the avoidance of solid waste,” Bristol said.
According to Bell's website, Bell’s recycling program reached a diversion rate of 83% in 2020. When including spent grain sent as cattle feed, the rate ballooned up to 99%.
Above the large holding tanks of the facility is another sustainable measure: an 8,000 sq ft plant-lined living roofing to provide greater insulation while catching and repurposing water runoff.
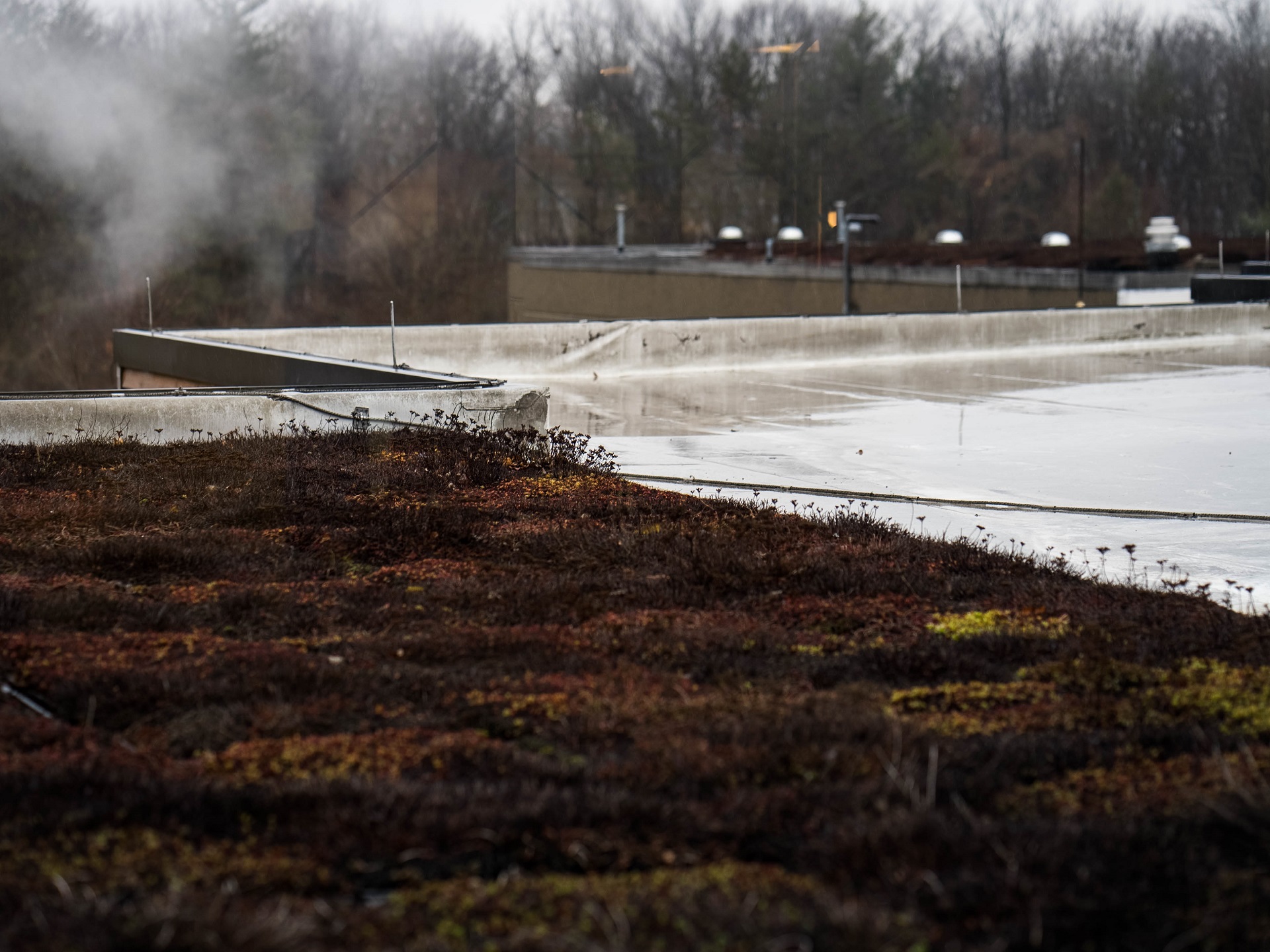
“We are always looking for ways to reuse water not only for economics, but also for an environmental responsibility standpoint to make this brewery have less of an impact on our local environment,” Bristol said.
Future Plans
Looking ahead, Bell’s strives to combine its data sources into one cohesive unit, combining Manufacturing Execution System (MES) and Enterprise Resource Planning (ERP) software data with lab information.
“We are looking into real-time monitoring of fermentation, coming down from fermentation being a matter of hours. If we can shave hours off of the amount of time beer sits in a tank it ultimately turns into cash as we are able to rotate things faster,” Sippel said. “There is a lot of data we can act on, and it is just a matter of building that out, acting on it, and adding this to the process.”
Attendee Thoughts
Coming up from the production floor staircase to the main concourse, there was light —and beer— at the end of the tunnel. Concluding the tour, attendees were treated to a well-deserved sample of Bell’s offering as the brewhouse opened up for networking.
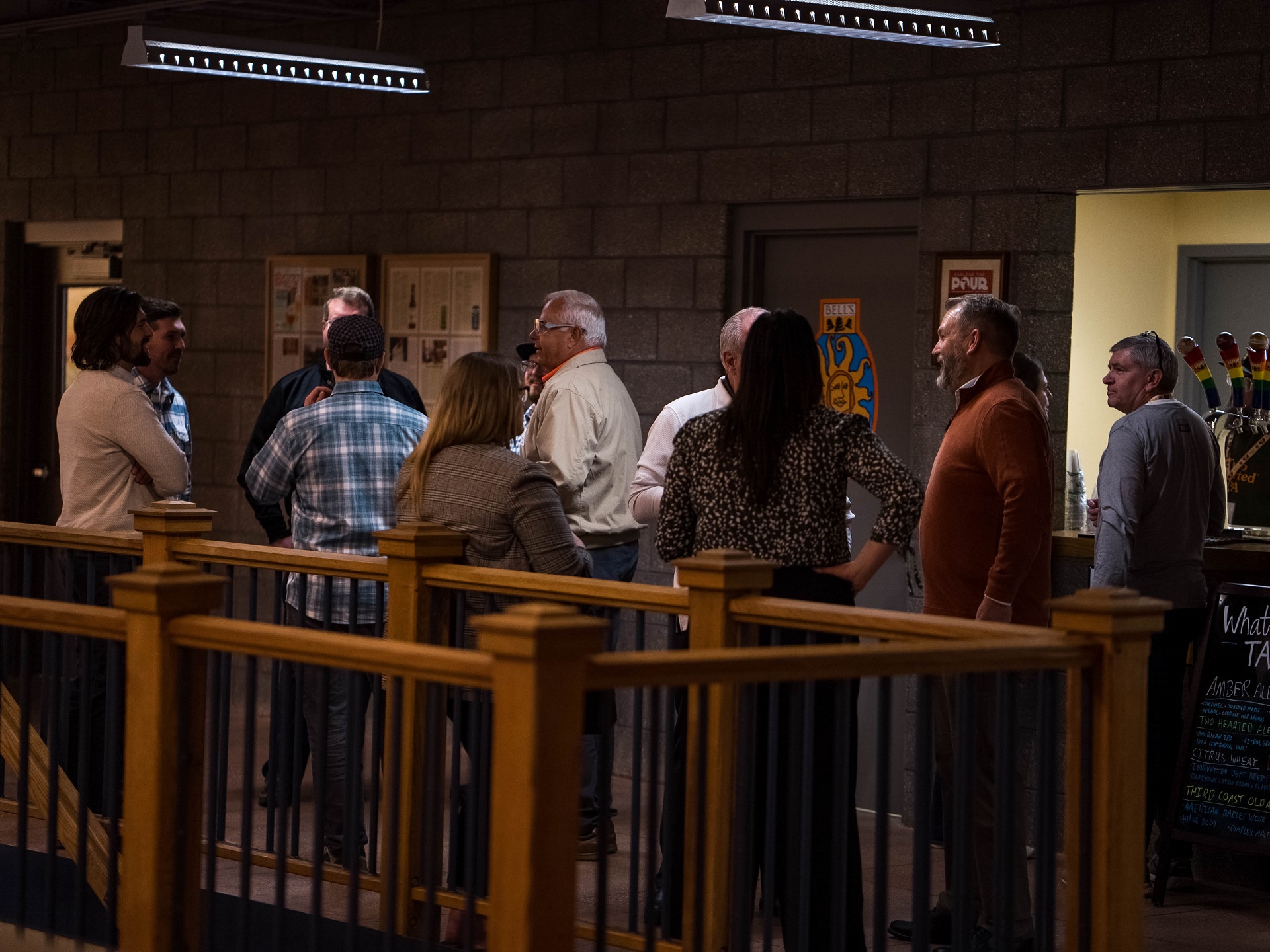
AVB director of business development Mike McIntyre and AVB project superintendent Ben Lawson were part of the over 50 attendees of the event.
“It was really cool to see on a big scale all of the automation in how they pump out so much beer in a quick amount of time. All the bottling lines going and going was really cool to see up front and center,” McIntyre said. “It was also good to see how good Bell’s is to the community as a large employer here.”
Lawson said he liked how organized the brew making processes were. “The culture here also seemed very positive with the [Bell’s] staff,” he added.
“We’re so grateful to Bell’s for their strong contributions to the Southwest Michigan region,” said Bronwyn Drost, Senior Director of Economic Development at Southwest Michigan First. “Not only does Bell’s participate in a variety of economic development initiatives designed to uplift our community, like a local sustainability group, this Industry 4.0 initiative, the movement to make childcare accessible to all, a regional Employer Resource Network employee retention program— and the list goes on—but they do so in such an open and collaborative spirit that genuinely engages businesses across a variety of sectors. Bell’s is a true jewel in our community.”
To schedule your own tour of the Bell’s Brewing facility, click here. Looking to join the next Automation Alley event? Visit our event page.
Sign up today for a free Essential Membership to Automation Alley to keep your finger on the pulse of digital transformation in Michigan and beyond.