At the Michigan Manufacturing Technology Center (The Center), our team enjoys the opportunity to visit clients in their facilities. Seeing the business in person gives us a well-rounded understanding of the current state and where we could potentially help the company improve.
When we engage with clients, the discussion often centers around performance numbers. In all cases, the journey toward continuous improvement starts with the existing condition of operations; it is more than just seeing the plant, we also need to look at the data being collected.
Finding Gaps in Data
Profitability is most often a common topic to talk about with our clients (for this discussion, we’ll use gross margin). Let’s do a little example to show the full picture.
In this example, let’s say the client’s gross margin is 20% and the minimum they quote is 25%. This begs the question, where did the 5% go? Putting it in dollars, for a $10 million company, we’d ask where did the $500,000 go?
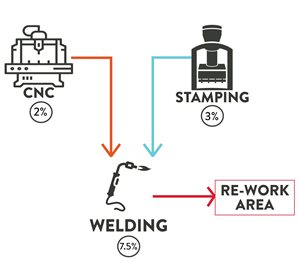
In the graphic (above), we see three operations, where stamping and CNC machining production flow into welding. Many times, a manufacturer’s operating systems don’t give insights to see the direct labor properly. This can create rework, quality defects and other errors which then cause the welders to “fix” the errors (like burs) in the re-work area, putting a drain on labor availability.
Read more here.