As many manufacturers begin to reopen plants across the country as lockdown measures begin ease, ensuring the safety of workers is critical. From appropriate personal protective equipment to maintaining physical distance from other employees, this is an unprecedented time with the pandemic and many manufacturers are not sure what steps to take to ensure the safety of workers in the time of Coronavirus.
There have been many different solutions proposed and implemented already. Due to COVID-19, it has become the new normal to conduct temperature checks of each employee, practice social distancing by ensuring employees stay six feet apart, and keeping track of cleaning efforts to sanitize stations more frequently. Some have even staggered shifts to avoid having too many people on the plant floor at one time. But many manufacturers are looking to technology for a more permanent solution. One such example is the use of wristbands that vibrate to alert a worker when someone is too close. This method may work, but it’s not incredibly reliable and doesn’t help with contact tracing.
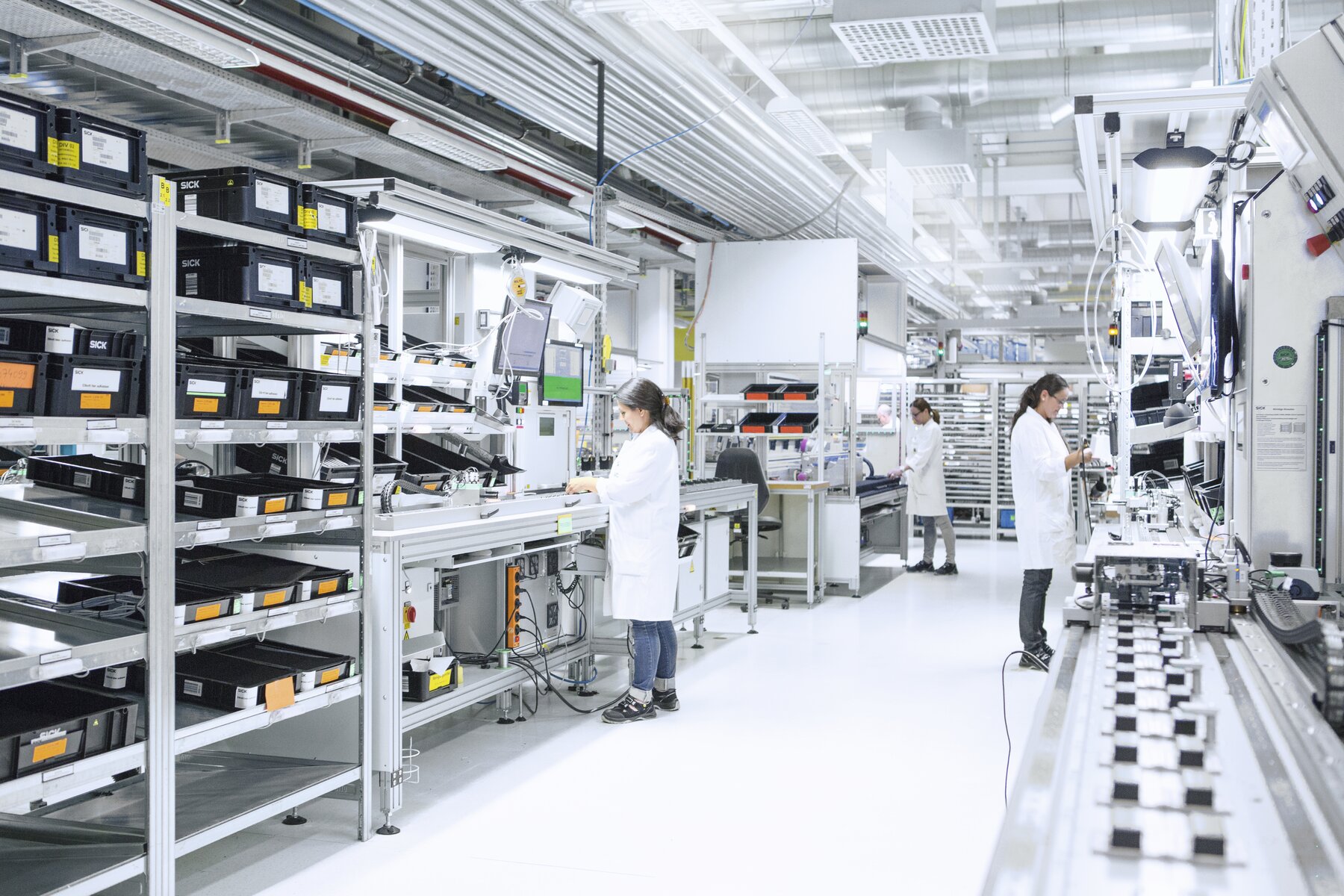
Maintaining Physical Distance
SICK, Inc. has a method that can provide reliable detection of people to ensure physical distancing measures are continuing to be practiced. Using LiDAR and track and trace technology from SICK, manufacturers can effectively detect people, products, parts, and more to ensure the safety of everyone within a plant. This technology enables people to effectively practice social distancing in a manufacturing facility while still operating efficiently.
LiDAR technology is commonly used on machines or mobile robots to protect people from harm. However, in this instance, LiDAR can be used to ensure people stay a safe distance apart from one another. By installing a sensor in each work station, it ensures a six-foot distance remains between people at all times. The LiDAR essentially creates virtual walls to form a three-sided box around a workstation. Markings on the floor will indicate the exact location of the virtual walls so an employee knows when they may be breaching the barrier.
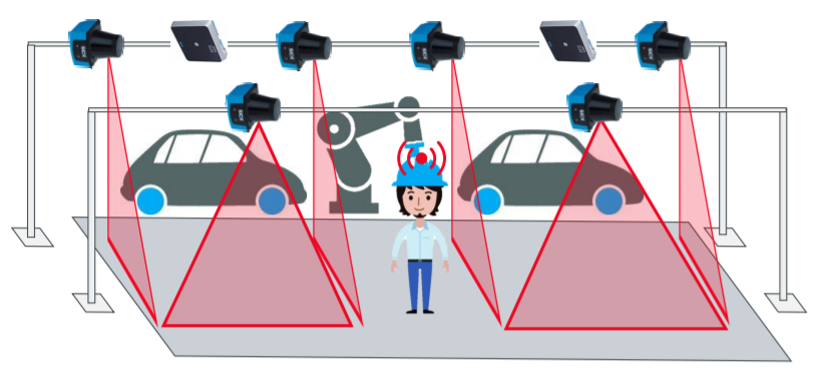
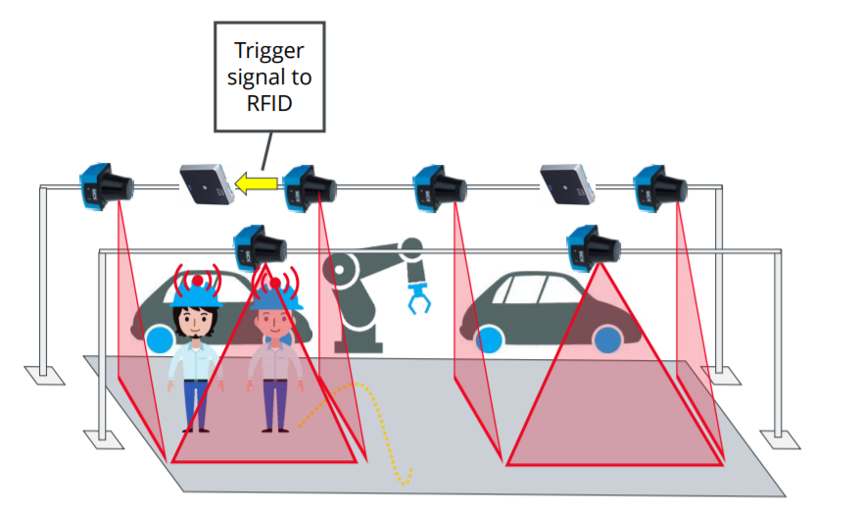
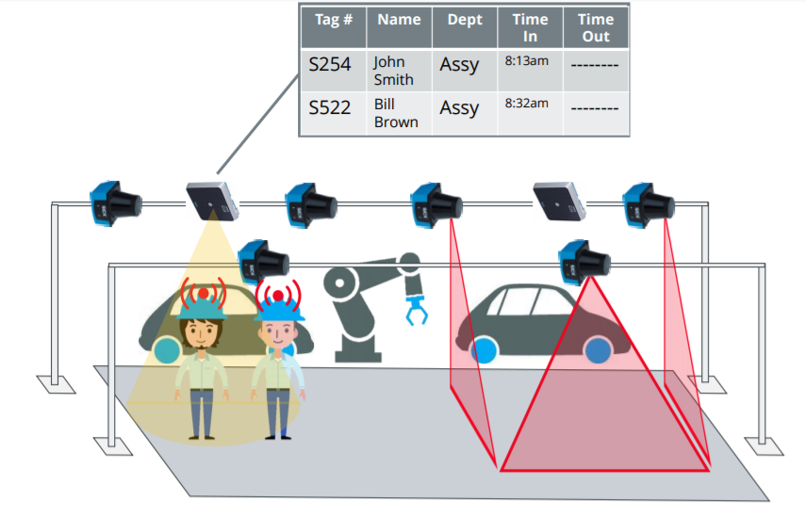
Tracking Throughout the Facility
RFID tags can be implemented on workers’ hard hats to track where each worker is traveling throughout the facility. Each worker will wear a passive tag that can provide data to the manufacturer via an RFID reader. This is beneficial once a person is identified as a health risk. RFID tags on hard hats can help identify and track everywhere a person went in the facility and also who and what they were in contact with to conduct effective contact tracing.
The manufacturer can set each worker to an assigned zone where they are designated to work. If they enter into a zone where they are not authorized to work, the plant operator can be notified so they can take appropriate action.
In addition, if a worker breaches a LiDAR barrier on an unauthorized workstation, the sensor will be notified and alert the RFID reader to scan. The employee in the workstation will also be alerted and can take appropriate action to maintain the needed physical distance. The RFID reader will collect data on each worker, which can include name, title, department, and time of scan.
These methods ensure that the manufacturer can maintain cleanliness and sanitation standards. The RFID reader provides data on how many people were in each work station at a given time based on the number of scans by the RFID tags.
These methods are new to every manufacturer, but may quickly become the new normal as times continue to change to adapt to the ever-changing manufacturing environment we are currently experiencing.
Looking for a solution to help with social distancing and contact tracing in your facility? Watch our webinar to learn more!