Nestled on the industrious Groesbeck Highway between 8 and 9 Mile Road in Warren, TubeCo is a tube manufacturer specializing in steel fabrication and cutting services. With over 50 years of experience, the company plays a critical role in the automotive industry, supplying components such as brake assemblies, fuel lines, headrests, dipstick tubes, and more.
As a recipient of the MEDC Industry 4.0 Implementation Grant, TubeCo introduced advanced sensors and a collaborative robot (cobot) to its operations—enhancements that have significantly improved daily processes while unlocking new business opportunities and operational visibility.
“I’m going to be very blunt and say, had we not implemented these Industry 4.0 items, we would not be servicing some of these $4 billion-a-year companies—companies that cross their T’s and dot their I’s on every little thing,” said TubeCo Vice President Matthew Peleman. “It’s just a fact.”
The grant enabled greater visibility into operations, Peleman added. “We’re trying to become a more data-driven business because we’re growing our staff and infrastructure.”
Some of TubeCo’s production machines even predate World War II—a testament to the enduring consistency of tubing manufacturing over the decades.
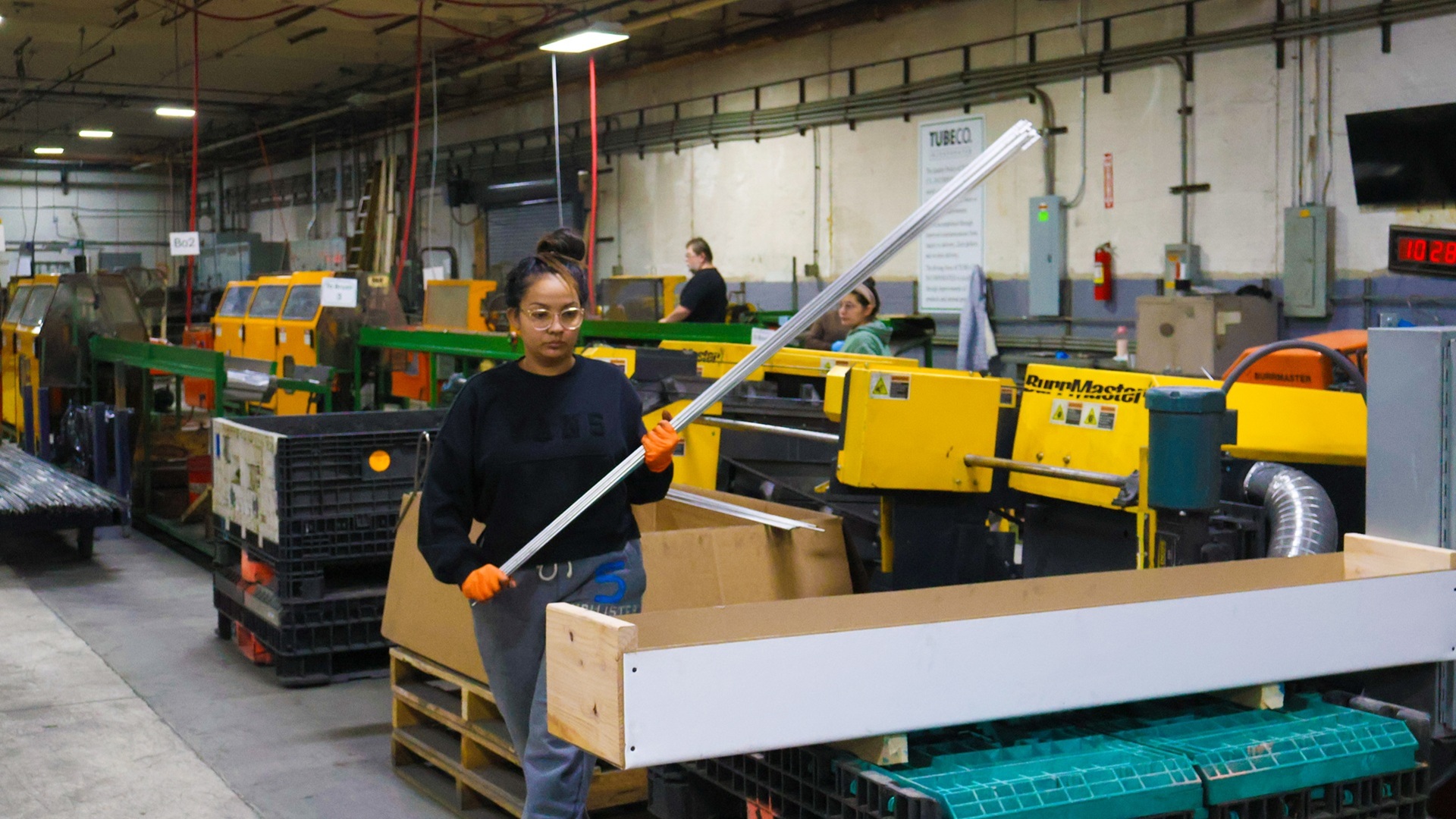
“We have a lot of pre-war machines. That’s not to say we don’t invest in upgrades, but tubing standards rarely change,” said Peleman. “These machines are extremely mechanical—there are literally no electronics—so we had to find a way to pull production data without relying on just pencil and paper.”
That challenge became an opportunity. Using Raspberry Pi computers and an array of sensors, TubeCo brought its legacy equipment into the era of Industry 4.0.
The key? Leveraging another Industry 4.0 technology—artificial intelligence (AI).
“To be honest, all I had was an idea about how to extract the data. I opened up ChatGPT, told it what I wanted to do, and it gave me a cursory plan to accomplish it,” Peleman said.
Guided by that AI-generated plan, Peleman and his team built a dashboard that tracks uptime, downtime, and cycle times across the factory floor.
Identifying quality issues has become significantly easier. “When a large customer comes to us and says, ‘Hey, you need to reject 10,000 parts because we found a huge quality concern,’ we can now go back and show there was no tooling issue. We can provide reasons. The proof is automated—we no longer have to dig for it,” Peleman said.
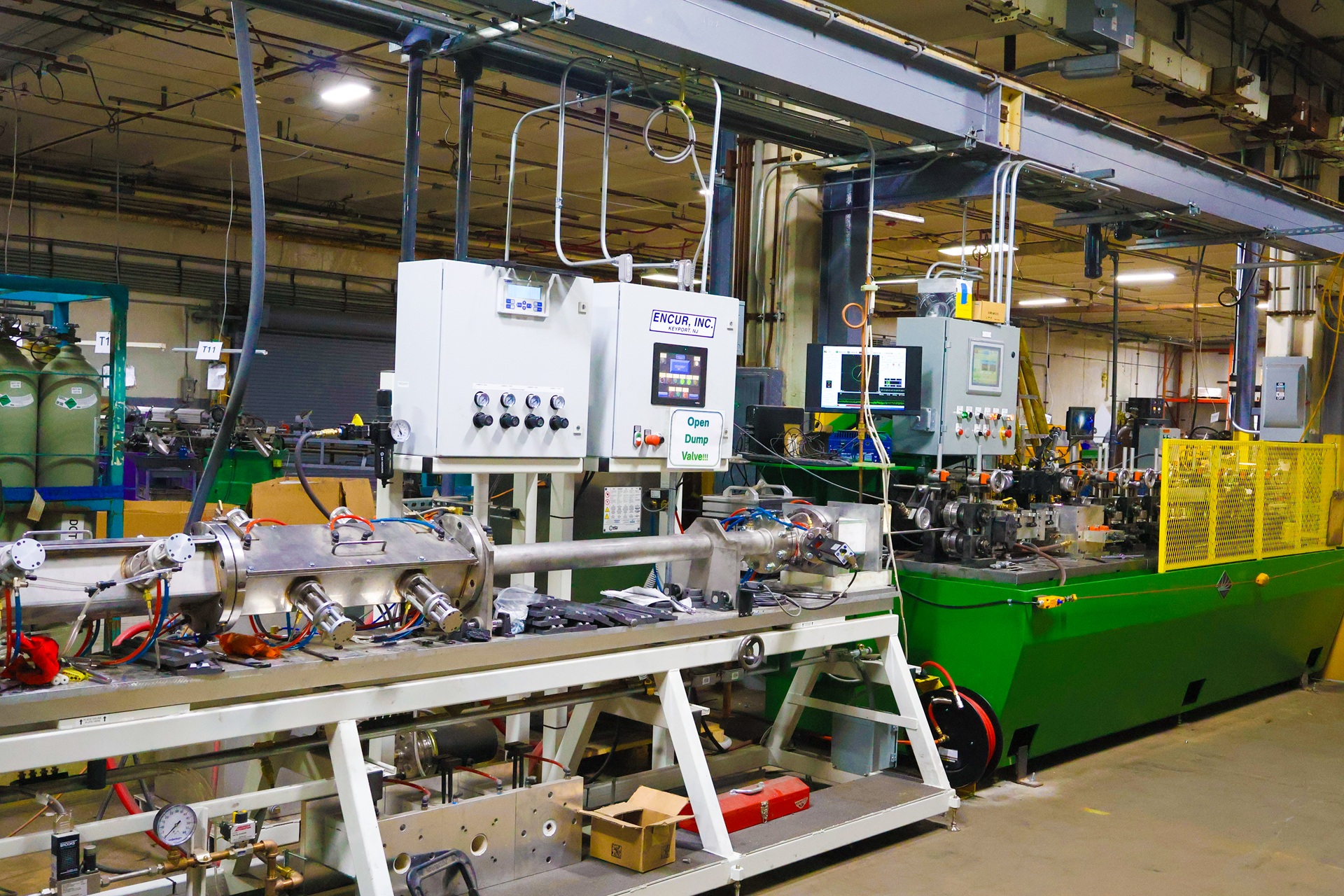
For more information about the Industry 4.0 Implementation Grant and how to apply, visit https://www.michiganbusiness.org/industry4-0/grant.
“Implementing new technology is not easy. It’s not cheap. But I think we’re doing a good job,” Peleman added.