1. Mindset Shift
The manufacturing industry is the cornerstone of all successful economies. It is the keystone sector for societal well-being and economic growth. It also has proven to be a major driver for knowledge creation both applied and theoretical. To maintain the engine of prosperity, the manufacturing industry must lead the digital and green revolution. This revolution is a comprehensive shift in understanding of new technological developments, when to use these technologies, what is appropriate in terms of investment, and how to be efficient and effective in using digital technologies. It also entails identifying the cultural workforce development and training needs required to better utilize digital technologies and be a true player in Industry 4.0.
The Fourth Industrial Revolution, or Industry 4.0, describes the socio-technological landscape transformation through digitalization of the manufacturing sector. However, at its core, Industry 4.0 fundamentally refers to the entire eco-system encompassing and including the technological concept of cyber-physical manufacturing systems. It is a development where every system comprises of a counterpart virtual system which truthfully represents the elements and dynamics of the physical system. The virtual counterpart is ‘born’ early in the beginning phases of system development, and runs along its lifecycle. The virtual system is data connected and enables the end users to interact with it, helping translate various control strategies to the physical system. The concept is now also referred to as a digital twin.
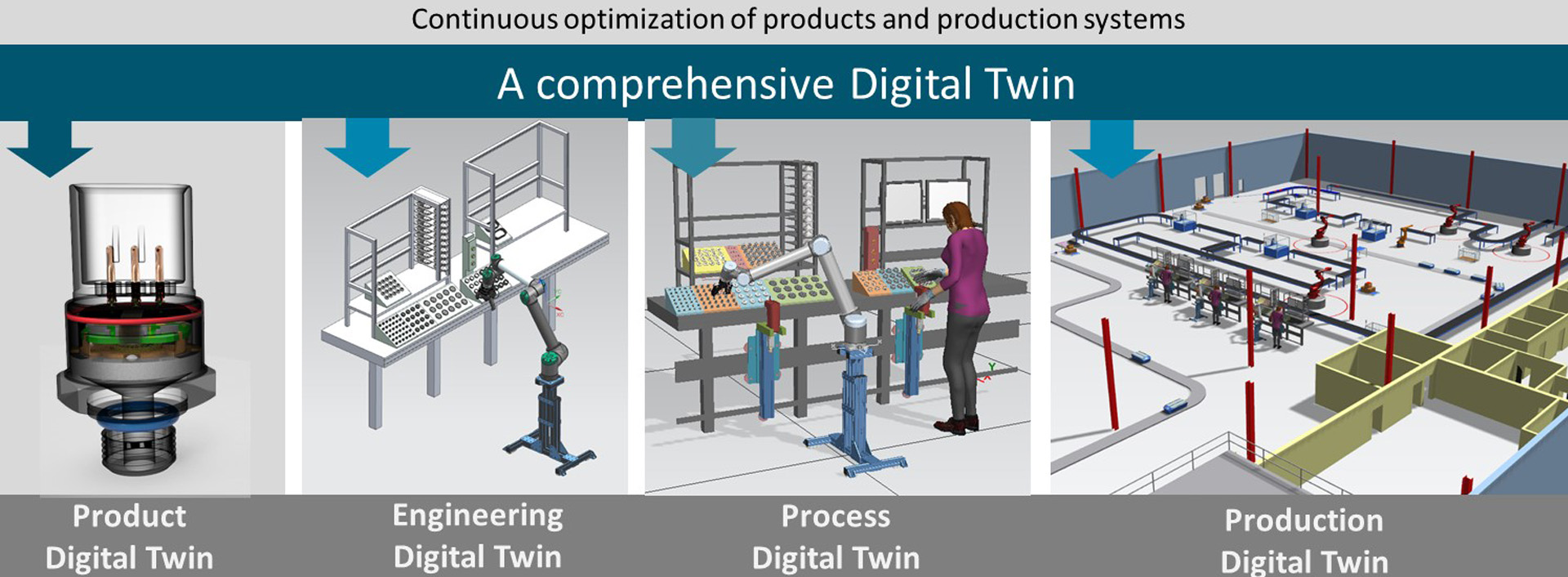
The developments in mindset shift can be explored along the following three dimensions:
1.1 Mindset Shift for Manufacturers
At the manufacturing system level, a digital copy of a physical system makes it substantially more controllable, predictable and adaptable to changing situations. The resulting system promises reduced material wastes, reduction in downtime and an ability to virtually test a future production strategy with an unlimited number of metrics. Market fluctuations and other environmental factors can be readily integrated and investigated with virtual (simulation) models. This allows for long-term projections of system performance and possible ways to accommodate them. This, in turn, helps manufacturers to re-adjust the actual system dynamics to quickly and effectively get aligned with new changes.
An example of beating strong competitors through software-based products is Tesla, the world’s leading company in electric cars. Tesla recently surpassed the automaker Toyota to become the world’s most valuable automaker in terms of market capitalization. Its value exceeds the value of General Motors and Ford Motor Company combined. How did this development against traditional automakers happen so quickly? One of the answers to this is Tesla’s strategy to develop cars as a software-integrated product. By having this feature, the company can transform and upgrade the vehicle software frequently, adding features and fixing bugs, resulting in a better user experience.
Assessing the market dynamics, GM and Ford have also responded to the emerging trends. GM plans to roll out a software platform named Ultifi based on the company’s current vehicle intelligence platform (VIP). The move will enable over-the-air updates and greater access to subscription services for vehicle owners. It will also provide drivers access to the functions of a vehicle resulting in greater safety, reliability, better and continuously improving user experience.
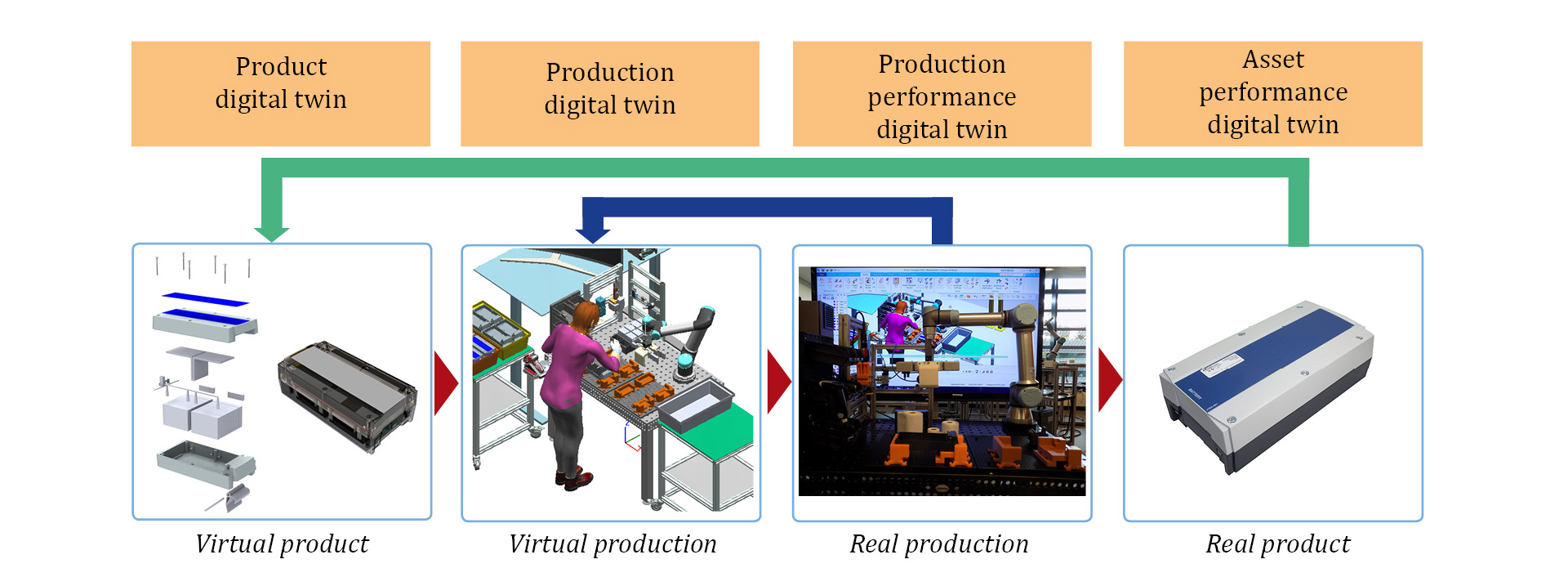
Another good example of the needed mindset shift in manufacturers is from Siemens Digital Industries that offers a complete PLM (Product Lifecycle Management) to develop manufacturing systems as digital artefacts. The digital models or artifacts contain all, or at least, the maximum details of the desired performance and behavior of a manufacturing system. Even before building the real system, and making any serious investments, the manufacturers can build a complete system in the software environment, run it virtually to evaluate its performance and align it with the organization’s needs. They can also integrate hardware emulators with the simulation and analyze and optimize its hardware-in-the-loops performance. The result is an accelerated development cycle, error-proof design and flexibility to reconfigurability.
These are not isolated examples. While computer simulation has been a large part of engineering design and manufacturing for some time, the convergence of all these digital technologies for a high-fidelity digital twin is increasingly becoming the norm in many industries.
1.2 Digital Transformation for End Users
A software-first mindset enables manufactures to upgrade their product and improve their user experience long after sales, by retaining the ability to upgrade the software element of the product. We already discussed the example of Tesla that used this as a major competitive advantage, while GM is on its way to facilitate its customers in this regard. This type of transformation is already a part of our lives with personal computers and Apple’s iPhones, which constantly upgrade software. By continuously analyzing the needs and expectations of customers, companies are transforming the end-user experience by merely offering an upgrade to the software, strengthening customers’ trust and satisfaction.
It is important to understand that customer needs and expectations are changing. This is partly due to best-in-class companies that are striving to offer customized and user-centered experiences. Amazon, Uber and Starbucks are a few examples that are catering the end users’ experience in their business intelligence. Other companies, and also B2B companies have to realize the needs and expectations of their end users. The end user experience is not something limited to B2C companies, but B2B companies also have to realize the importance of human touch along their software transformation journey. A software transformation integrated with human needs and emotional behaviors is likely to achieve loyalty and greater satisfaction.
The new wearable technologies for visualizing and interacting with the digital information also need to be considered along a software transformation journey. Its examples are virtual reality headsets, augmented reality devices, smart watches and smart glasses. Similar to smart phones, these devices are likely to become an integral part of our lives in the future. Microsoft is already offering augmented reality experience of its Microsoft Office tools for immersive and collaborative operations. It also results in reduced travel and increased efficiency.
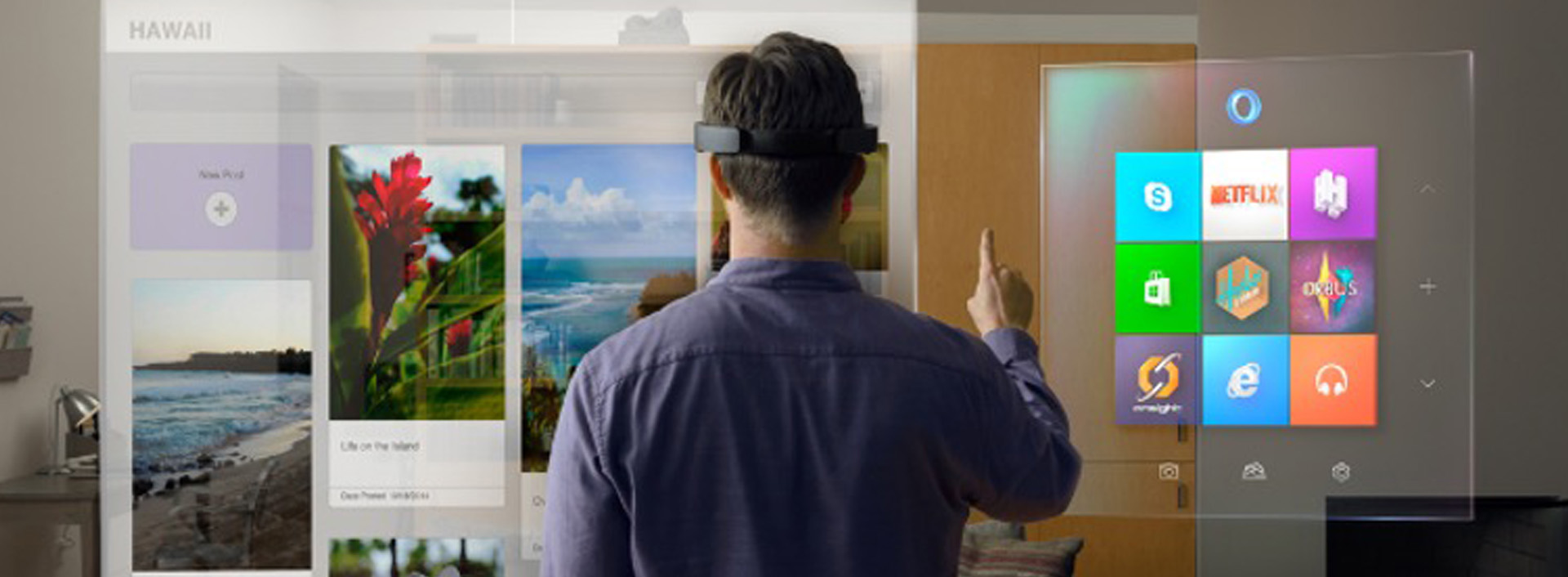
The world’s leading social media network Facebook is also working to offer a future immersive experience to its users. The new immersive environment is a network of 3D virtual worlds enabled by virtual reality headsets and is aimed for social interaction. With 2.94 billion users, Facebook has rebranded itself as Meta. However, it will not remain limited to entertainment and social interaction, but the results will also shift towards manufacturing. NVIDIA and BMW are already working to develop metaverse via realistic 3D virtual factories visualized through VR headsets.
1.3 Transformation for Policy Makers
This section presents a digital transformation skills requirement framework for the near- and long-terms. The goal is to have an Industry 4.0-ready workforce which is aligned with digital work environments such as digital twins and metaverse. As per World Economic Forum, most jobs that our future generation will do have not yet been created.
Considering the example of a generic product development (PD) process, it all starts with the analysis of “what to build.” This transpires in the form of customer needs assessment through demand modeling, online surveys or meeting with focus groups – most of which are increasingly being run virtually. Then we see a departure from traditional product development processes. There is a transition to digital twins integrated product development where a precise, virtual copy of machines or systems are born alongside the lifecycle of the physical system. The sophisticated computer models backed by the data collected from sensors in real time, can mirror almost every facet of a product, process or service.
We need a workforce that is adept in all these steps in the rapidly transforming PD lifecycle. Universities and trade schools need to embed Industry 4.0 tools and digital twin concepts directly into their curriculum. Familiarity of workers with various simulation tools and data connectivity aspects is crucial. There needs to also be a concerted effort from local governments in ensuring that small manufacturers are familiar with this change in how engineering design and manufacturing is going to be implemented. This will help them survive in the new ecosystem and compete effectively. Local, state, and federal governments need to provide avenues including grants as a means for this transformation that is needed in the workforce and small businesses.
To address the present and future needs of workforce, companies need to work with policy makers to:
Rethink education systems: There is a wide gap between the knowledge being transferred to the students at universities and the changing needs of businesses. Most education systems are based on 20th century’s needs. The Fourth Industrial Revolution will construct several new cross functional roles for which new skills are desired that need to be integrated into education systems.
Incentivizing lifelong learning: Upskilling and reskilling of employees can be enabled by leveraging digital technologies. Countries affected by ageing population particularly need to enable and ensure lifelong learning opportunities for its available workforce. A good example is Denmark where training incentives by the government have enabled greater employment mobility and mid-career transition taken as a norm.
Cross industry collaboration: Education, industry and government also need to collaborate on talent issues, skills requirements and available talent pools to form a future view of skills and formalize strategies for how to upskill the workforce.
2. Business Models
Despite much interest in academia, most large manufacturers have only made incremental strides in digitizing their core offerings, such as creating a digital sales channel or using digital tools to improve internal operations. But a need is becoming urgently evident to shift from digital interfaces of the products being offered by a company to a fully digital business model.
As per Mckinsey, a user-centered digital transformation of a business can make a 20-50% increase in revenues. They also suggest that 73% of customers are more likely to make purchases from a business channel that addresses them by their names. Personalization and achieving a customized batch size of production has never been more important to the manufacturing industry.
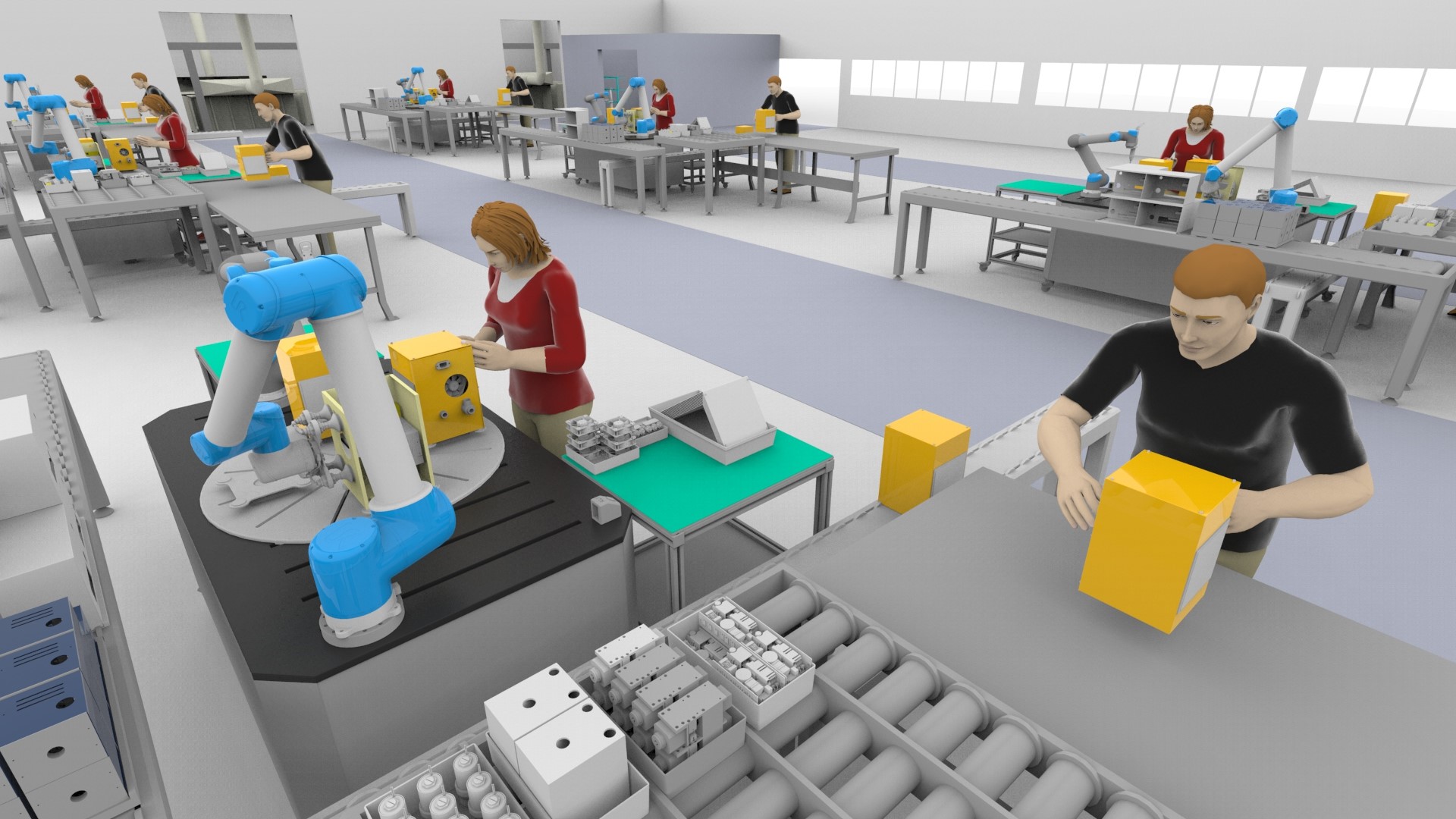
Metaverse is another example of immersive digital transformation that requires a business model shift. It necessitates getting aligned with new ways of interacting with others through innovative ways of conducting meetings, and facilitating collaboration. NVIDIA’s Omniverse platform is an integrated environment of a wide range of virtual tools for creating a high quality, realistically rendered, data connected, immersive simulation of factories. An advantage of such an intelligent simulation is that it can simplify the path towards human-robot teams. Enabled by physics-based simulations, and AI brains, the robots can learn from their environment and those learned brains can be loaded onto a real robot. Thereby the manufactures can not only achieve realistic simulations of their manufacturing facilities but also can use the simulation (or digital twin) as an intelligent control and training platform.
The digital disruption was brought to the forefront by the COVID-19 pandemic that forced people to work remotely, making the best use of digital technologies. As per The Economist, 65% of the workforce will continue to work remotely or in a hybrid fashion even after the pandemic is over. We definitely need to better understand how it will require different approaches to accomplish tasks and to create a balance between work and social life. More importantly, what is an optimal mix between in-person interaction between team members and interaction through virtual channels.
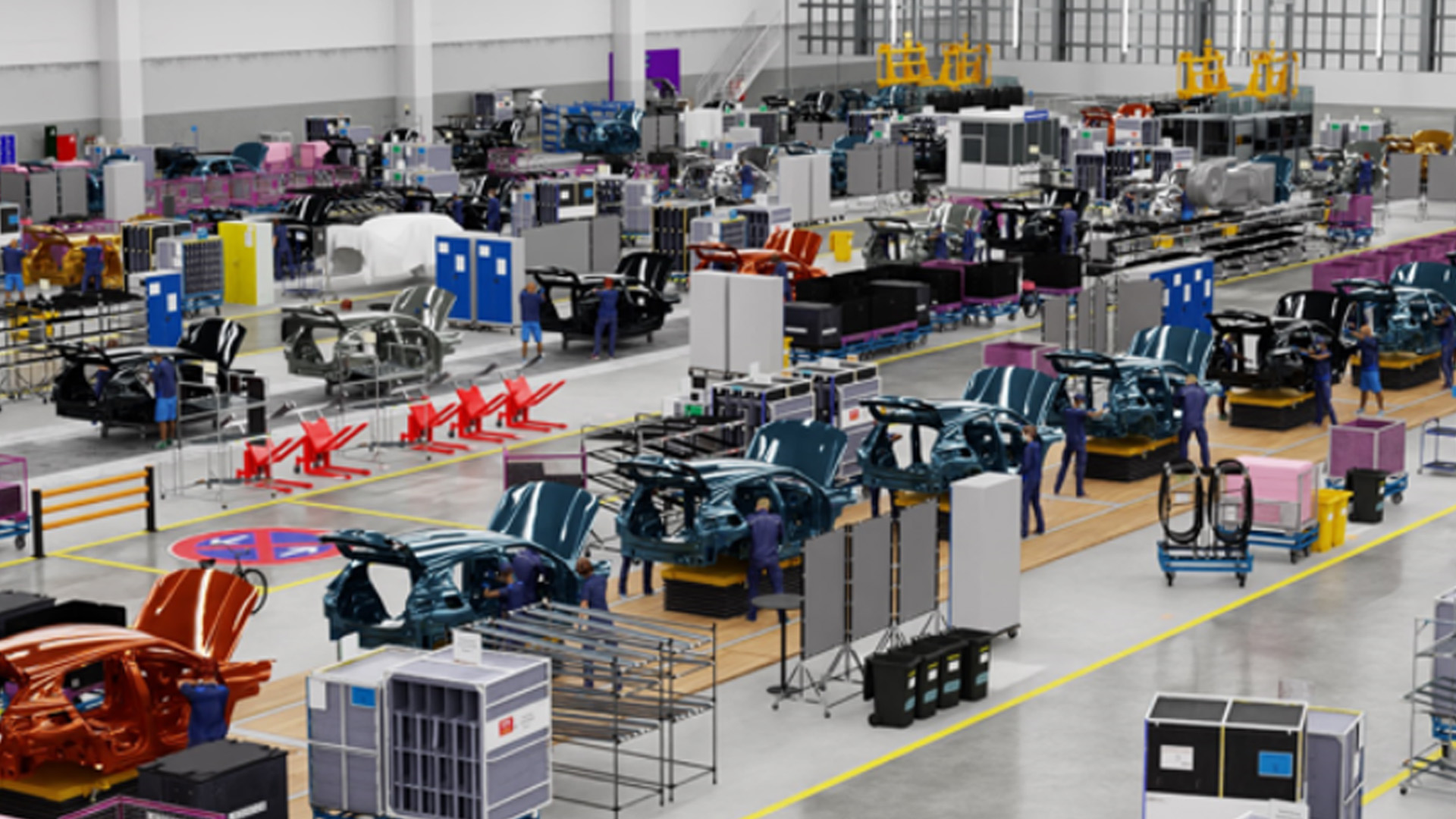
Digital Tools & Innovation
This section will look at a framework to infuse innovative technologies and digitally transform the functions of designing, developing, using, maintaining as well as aligning the end-of-life plan of a product. Various new technologies becoming available today are discussed. Additionally, an outlook is presented for the near future and also for the long term.
The present and anticipated developments in software transformation can be seen in three phases of a product’s lifecycle: design, development, and operations.
3.1 Design phase
The fast development of virtual models is reducing system development time, and design and redesign strategies can quickly be implemented into the real world. An example of this is in the field of robotics and collaborative robots. These robots are desired to be flexible and adaptable. For every design change in the product or system, the manufacturing system needs to be safety validated, optimized for layout, and adjusted to achieve an optimal workstation. Virtual models are essential for this and must incorporate the advancements in robotics.

KUKA and Universal Robots are two leading global robotic manufacturing companies. For fast validation of manufacturing systems using their products, the companies are offering software solutions that are intuitive, easy to use, and work easily with drag-and-drop features. The robotic tasks are programmed with user friendly graphical interfaces. Hence the total time to design the manufacturing cell has been reduced to less than an hour compared to the more conventional approach which used to easily take several days. Another interesting aspect is that these virtual models developed during the design phase can continuously be used during development and for any reconfiguration. The virtual environment creates robot programs that are transferable to the physical system.
3.2 Development and Operation Phase
A physical manufacturing system may consist of several sensors, actuators, robotics, machine tools, and material handling devices. Real-time performance monitoring of all this hardware will enable a better view of the hardware performance, malfunctions, and remote adjustments. Software provider PTC is offering a comprehensive solution of hardware data connectivity with its virtual system that is remotely accessible. The performance of the system can be monitored in real-time on a dashboard that shows key system metrics.
To offer intuitive user interface for the end users, an augmented reality (AR) feature can also be enabled that allows a user to view system performance with the help of a wearable AR device. The user can visualize the information and can interact with the hardware to pass any instructions.
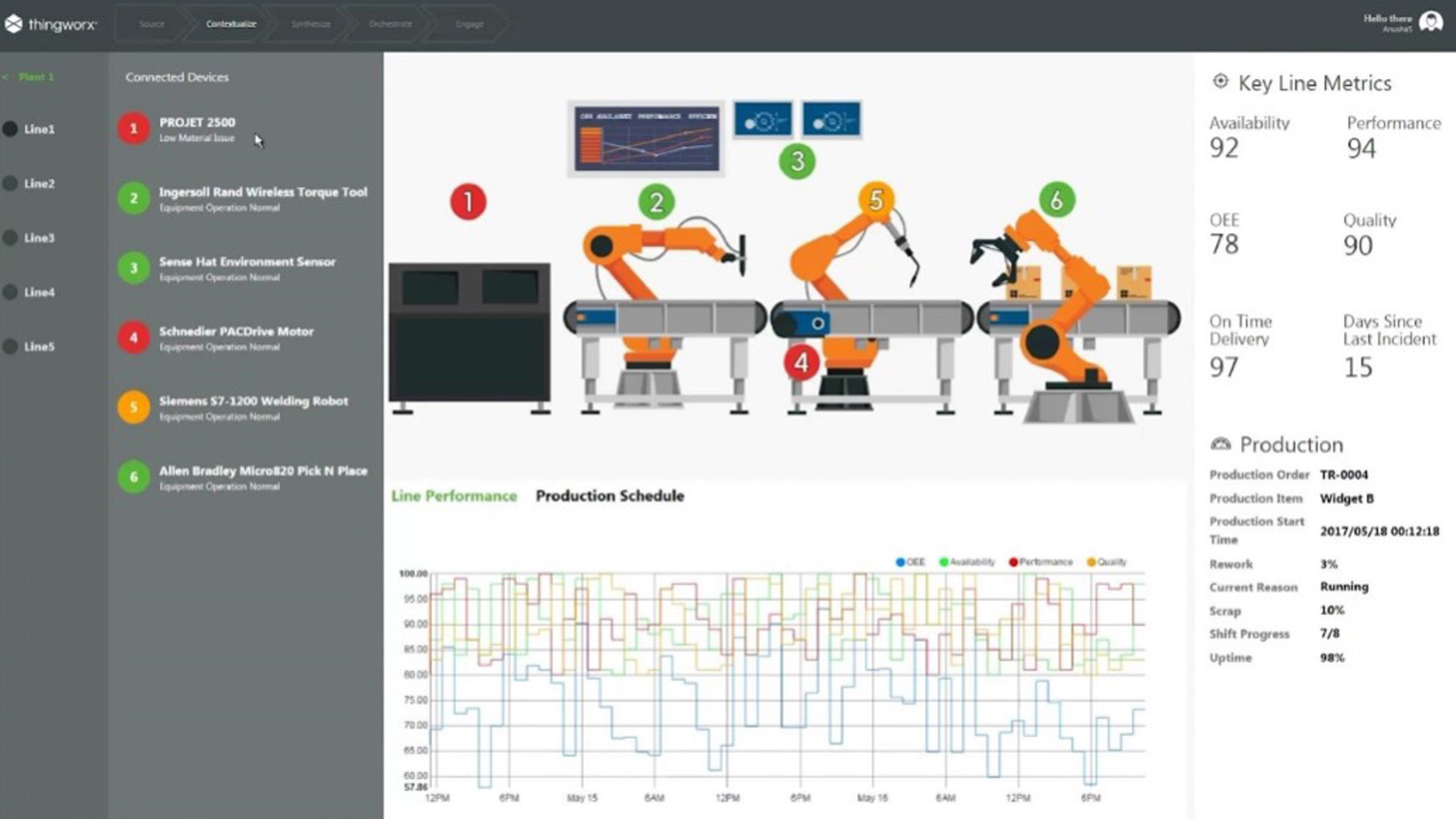
Figure 7: Dashboard of IoT connected hardware
In all these above developments, high-fidelity, high-volume data is at the backbone of system performance. All machines and associated hardware continually produce enormous amounts of data. A business can gain a huge competitive advantage by making sense of this data and translating the effects onto future strategies.
The topic of making sense of copious manufacturing data has been in discussion for several years, but new Industry 4.0 developments are redefining those technologies and some of them are even evolving into new technologies and new technology intersections. For example, as discussed above, the combination of the Internet of Things (IoT), data analytics and simulation modeling has evolved into the technology of digital twins. Similarly, considerable developments can be made with the use of AI and machine learning algorithms and automating the process of data utilization. Machine learning combine with 3D printing, for example, has enabled the concept of generative design that results in less material consumption and faster manufacturing processes. While autonomous robots, combined with machine learning and safety technologies are helping realize successful human robot teams in many applications.
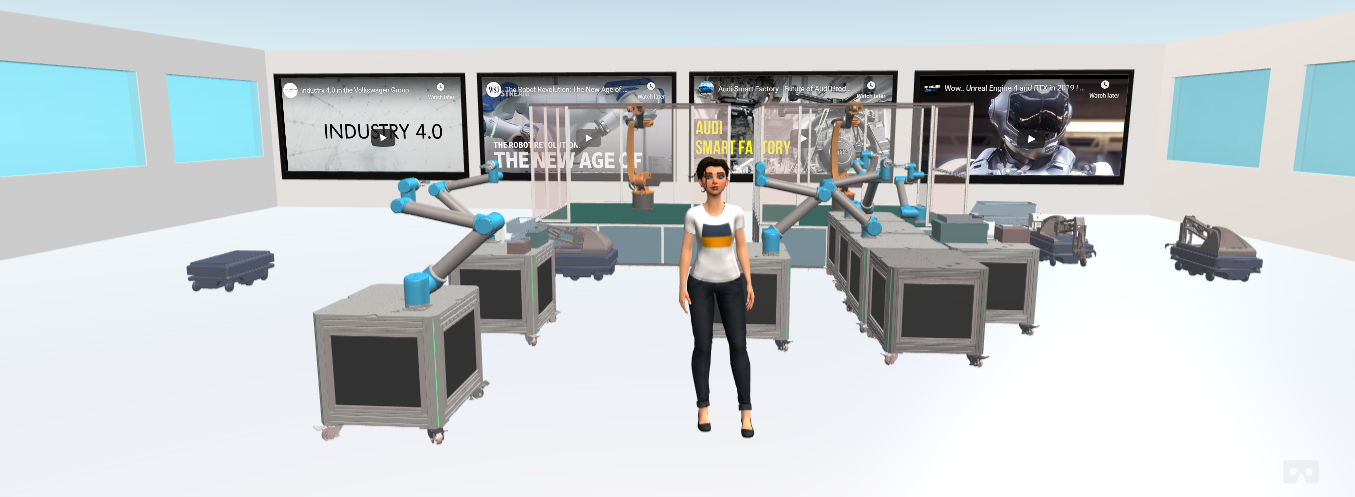
These developments will keep reshaping the technological landscape, however, getting a manufacturer’s mission and vision in full alignment with software transformation is a strategic step. Companies must get their goals and objectives aligned with the digitalization developments and strategize a roadmap. They must fully plan the scale, scope, investment, resources available, and workforce development aspects. They also must understand that these technological developments are happening at a rapid pace, and in the next few years, these technologies will be at a much higher maturity level than their present state. With software at its core, the future of smart manufacturing has even more potential than originally envisioned a decade ago.
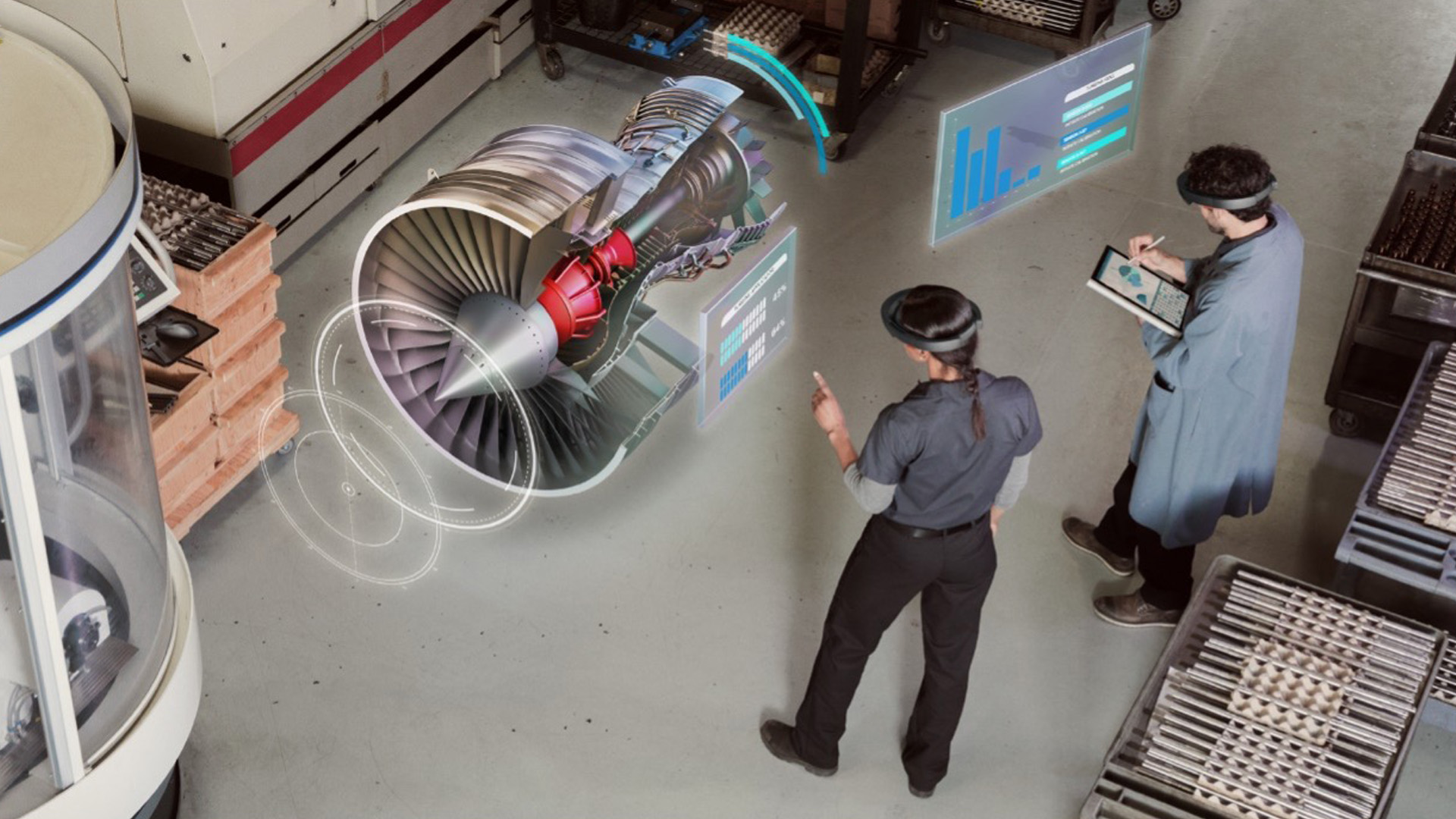
4. Next Steps
Advanced manufacturing is shifting towards a new paradigm. Historically, the new manufacturing paradigms have been realized through new market expectations and availability of new technologies that form innovative manufacturing systems to address market dynamics. The software transformation and software-first mindset is likely to achieve new forms of manufacturing systems that are more adaptable, easy to reconfigure and able to offer customized products.
The following table summarizes key list of considerations discussed in this paper and a way forward:
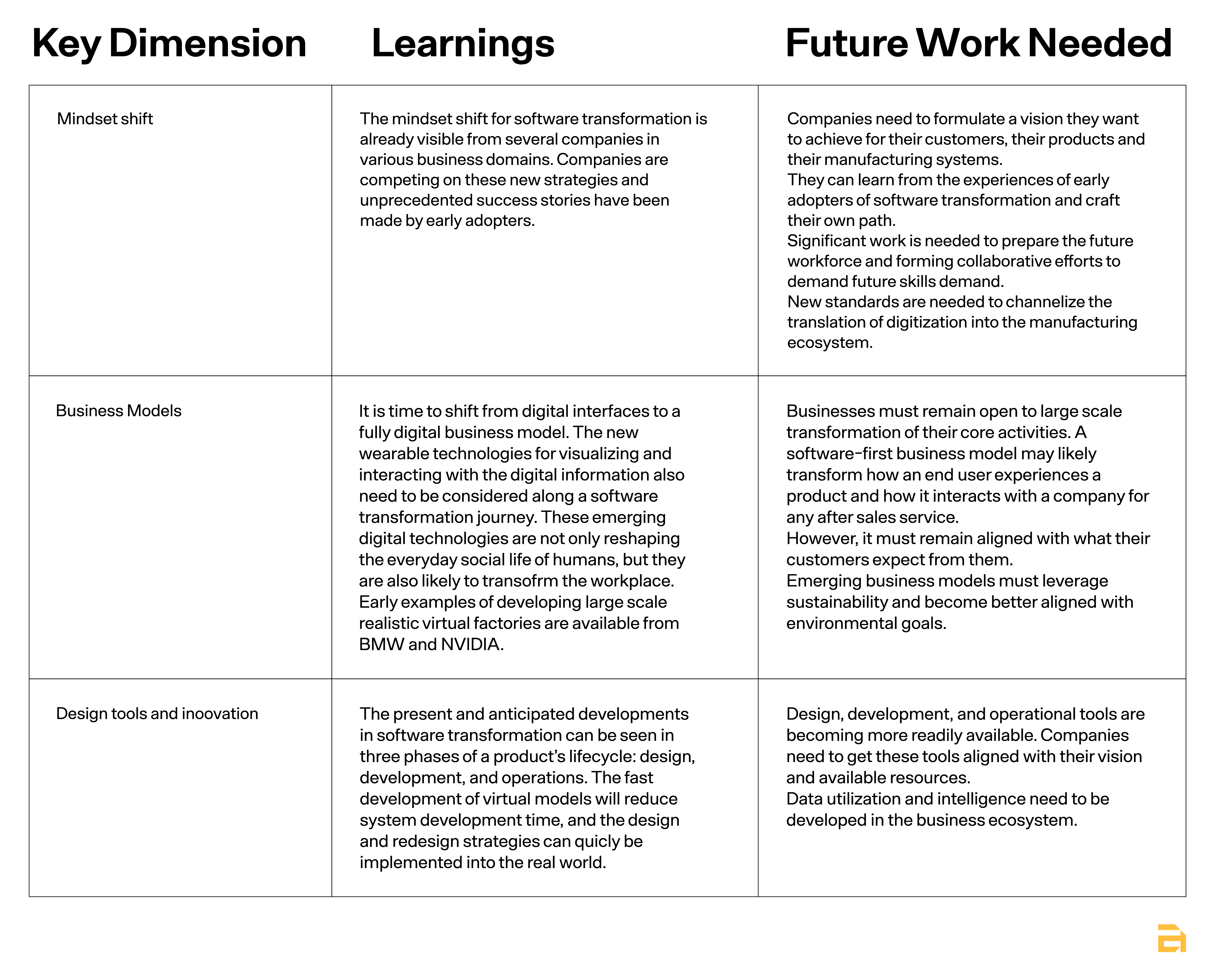